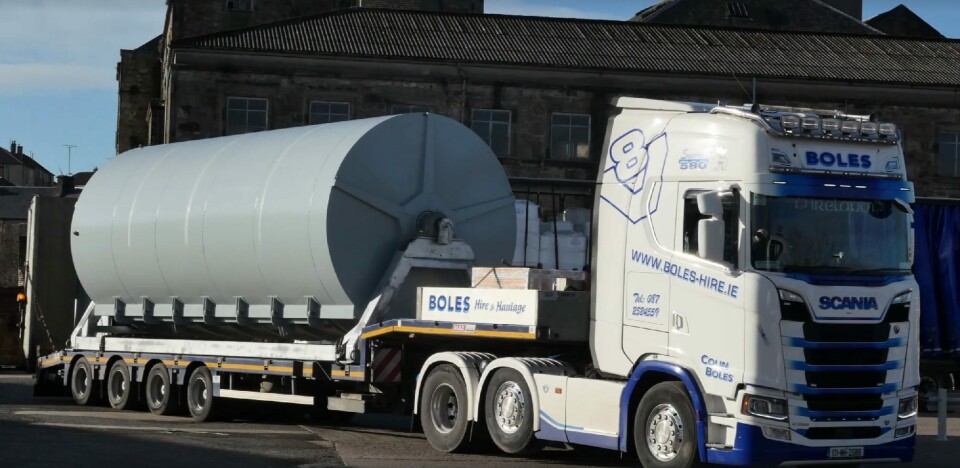
Knox hoping for net gains from washer investment
Aquaculture net supplier and servicer W&J Knox has taken delivery a much bigger net washer as it aims to “future-proof” its equipment in an era of ever-larger salmon cages.
The 56m³ machine has nearly twice the capacity of the two largest washers currently operating at the company’s Kilbirnie service centre, each of which is 30m³.
Managing director Dave Hutchens said the Irish-made net washer was a “substantial investment” that was required because nets were not only becoming larger capacity but were also increasingly being made of bulkier material.
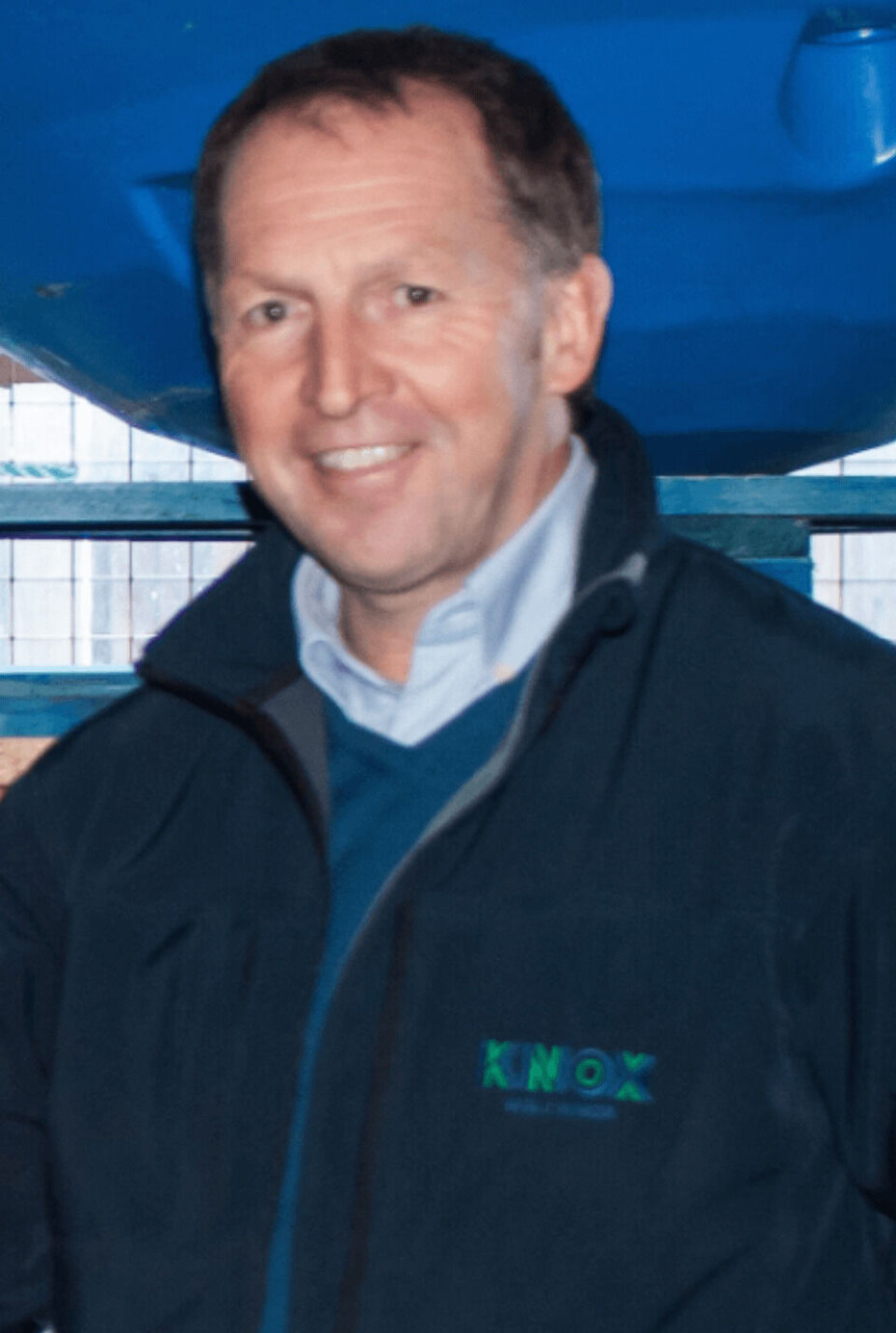
“A few years ago, 70 and 80-metre circle nets were fairly common. They’re still there but not so common; 100s, 120s, 130s are now the norm,” said Hutchens.
Moving from nylon
“Added to that, the industry is generally moving away from nylon nets towards the new HDPE nets which have more volume to them because the material has different properties to it.
“A nylon net is quite compact when it’s wet, whereas HDPE is springier, so when you go to put it into a net-washing machine it takes up more space compared to an equivalent-size nylon net.”
He said that about two years ago Knox increased the size of the doors on its washers to allow it to get bigger nets in, but that a bigger washer was needed because nets relied on a tumbling effect to get clean and a larger net would fill the washer with no space for it to tumble.
“That’s what drove us to get a bigger machine, but also in the not-too-distant future somebody’s going to put in a 160-metre net,” said Hutchens.
“We see that what happens in Norway trickles into Scotland two or three years later, and they’re already at 160, 200-metre nets in Norway, so it’s coming our way and we thought we needed to future-proof that.”
Article continues below video.
With Knox servicing around 1,000 nets a year at Kilbirnie, two 30m³ washers will continue to be used alongside the new machine, although a smaller 20m³ washer will be mothballed.
Knox supplies nets made to its specification by Garware Technical Fibres in Pune, India, and Hutchens is expecting to sell more HDPE nets than nylon nets in the future. These include the Sapphire Sealpro net used by Scottish Sea Farms and Cooke Aquaculture to protect stock from predators, leading to a reduction in the numbert of seals shot. Hutchens said there was now more interest in the nets after they had been proven over a full farming cycle.
Reluctance to use knotted net
“There was a reluctance at first because it’s a knotted mesh, rather than knotless, but Cooke Aquaculture have farmed full cycles now in these knotted nets,” said the managing director. “Garware developed a single-sided knot, so it looks like a normal knotted net but one side is slightly smoother than the other. That will be on the inside edge so that will be presented to the salmon.
“The outside edge is fairly rough still, which is probably where the success has come in terms of the seal defence, because seals have very sensitive snouts and when they come into contact with this they don’t like it.
“The Sapphire costs more than a standard nylon net. I think there was a reluctance early on – farmers wanted to see the value of these nets – but they’re very quickly paid for in terms of the value of the fish they do not lose to seal attacks.”
Stronger for longer
He said HDPE nets were also better for farmers who carried out frequent in situ net washing, because they retain their strength better than nylon.
“The HPDE has fewer fibres but they are much thicker, whereas nylon has lots of very fine fibres, and if you damage those with the washers then the fibres don’t work in unison with each other,” he explained.
“It’s much harder to break the bigger fibres in the HDPE. It’s a stronger product to start with but it retains its strength because it’s harder to break these individual fibres.”
Semi-closed containment
Hutchens said Knox was also looking to a future beyond nets by working with Garware on a PVC bag that could be used both to store freshwater for freshwater treatments of salmon and for semi-closed containment, although he stressed a lot of research and development was still required on such technology.
“You almost need to have an industry partner who’ll say: ‘There’s a site, there’s a cage, make a bag to fit it and we’ll try it without fish first, then maybe introduce some fish into it.’ The industry here really needs a development site where the likes of us can say, ‘Can we hire that cage for six months because we’ve got this bag we want to trial?’, unless you can get a partner. At the moment we don’t have that.
Marginal sites
“There are a couple of more forward-thinking companies that might take that approach, it’s just getting them on board and saying, ‘We can make it, do you want to try it?’ but a lot of them want all their cages full of fish rather than experimenting with something.
“This could be a way of utilising the more marginal sites. Because the salmon farmers are under pressure to reduce deposits on the seabed, so if they can collect the waste that’s collected in the bag and not contribute to that deposition on the seabed, that’s going to be a positive effect.
T”hey want to grow more fish but they’re not getting the licences, so if that enables them to produce more fish on their existing sites by reducing that waste then that could be the way they go.”