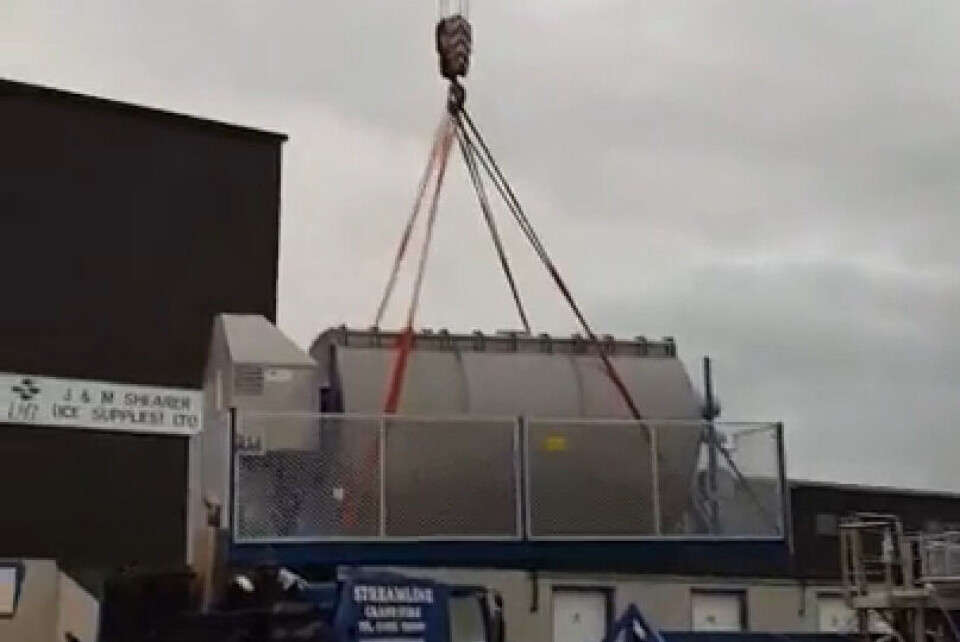
New washer, new name and new factory for Net Services
A company that manufactures and services nets for the salmon farming industry has taken delivery of the largest net washer in the country as part of an investment in bigger, more modern equipment.
Net Services (Shetland) Ltd has also changed its name to Mørenot Scotland to reflect that fact that it has been owned by the Norwegian Mørenot Group since 2008.
Managing director David Goodlad hopes the change will end confusion between the Shetland company and its subsidiary Net Services (Scotland) Ltd, as both will now come under the same name.
He said: “There are problems with suppliers because we’ve got two companies, and invoices get sent to the wrong ones and one thing and another.
“What we intend doing now is changing it over so it is just one big company with two departments, and that will be Mørenot Scotland.”
Mooring grids
Mørenot Scotland makes nets at its site in Scalloway, Shetland and mooring grids at its site on the island of Scalpay, on the eastern side of Harris. Both sites also provide net washing and servicing.
The company works for different fish farmers but Mowi – formerly Marine Harvest – is its biggest customer for grids and nets.
“We’ve sold between 30 and 40 mooring grids to Mowi over the last three or four years,” said Goodlad. “We’ve just sold the first one into Canada and the first one into Ireland.”
Extra staff
The Scalloway site has a full order book for environets from Mowi, in part thanks to work done by Goodlad to help develop the product. The environet is two nets stitched together, with one half always out of the water, drying. The salmon farmer has found this to be an effective, environmentally-friendly way to prevent fouling.
“All our production in Shetland just now is taken up by enviro circle nets. [Mowi Scotland seawater manager] David MacGillivray came to me because he’d been told by various net people it wasn’t possible [with a circular net]. He was sure it was. He showed me how he wanted to fit it to the cage and I then designed the net to fit. The first trial we put in the sea worked and we’ve produced about 70 so far, and our production is full until summertime and more.”
The company has taken on extra staff to cope with a growing workload. “We have 28 people employed just now between the two locations. I’ve just had a new start this week and there’s another one starting on February 4,” said Goodlad.
The arrival of the new net washer at Scalloway is part of a general updating of equipment, which Goodlad says is being financed through the firm’s own earnings without having to resort to funds from the Norwegian parent company.
“We’re upgrading all the equipment,” said Goodlad. “Some of it dates back to 2001 when we started. We’re getting newer and bigger equipment, because the nets now compared to what they were in 2001 are massive, so we’re having to change everything to suit the size of the nets the customers are using.
Biggest on the market
“We were replacing a 21m³ net washer with a 52m³ washer, the biggest one on the market, I think. It came a bit faster than I anticipated because I contacted the manufacturer in Norway and luckily they’d just finished a machine for Mørenot Hammerfest but they weren’t ready to install it so we got the machine and they’re now building another one for Mørenot Hammerfest.
“It’s now on site and it’s being installed and hopefully it’ll be up and running within a few weeks.”
Goodlad said the machine would clean bigger nets more quickly and efficiently.
“When you get a very big net packed into a small washer it takes a lot longer to get it clean because it doesn’t have the room inside to tumble around,” he explained. “Now we’ve got a bigger void the net can tumble around better so we should be able to get it cleaner faster.”
Shown dedication to area
Progress is also being made at Scalpay, where fire destroyed the company’s factory in April last year. A new building has been erected on the same footprint and is in use, although the firm is having to use a generator because mains power has not yet been reconnected.
Goodlad praised the architect and builders for the quick turnaround, and his staff for braving the elements. “My staff in Harris worked through the winter outdoors. They were limited some days in what they could do but they did really well – we kept every customer happy,” he said.
Goodlad believes the company has demonstrated its commitment to Scalpay after it expanded there in 2008.
“We got a lot of bad publicity when we announced we were going to start using the disused factory in Scalpay,” he recalled.
“We got some grants to put in new equipment and there were people who said we were just there to get the money and go. I think we’ve proved them wrong. We bought the building in 2017 and it took fire four days later and burnt down, and we’ve completely replaced the building, so we’ve shown our dedication to the industry in the area.”