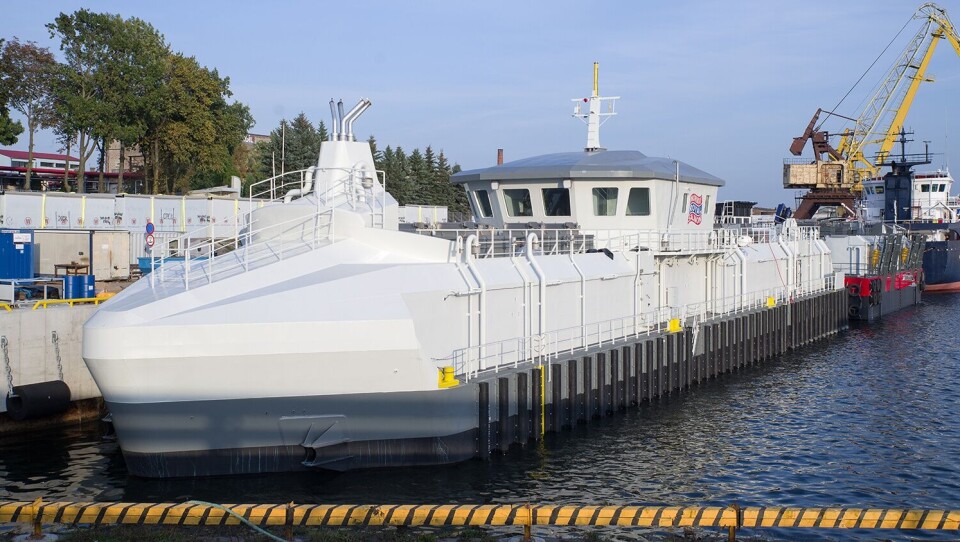
AKVA builds ‘toughest-ever’ barge for exposed site
Aquaculture supplier AKVA group has developed what it says is its strongest ever feed barge to Norway Royal Salmon (NRS) subsidiary Arctic Offshore Farming (AOF).
“This is the toughest barge AKVA group has ever made and it can handle ‘weather from all sides’,” said AKVA group project manager Kent Ims Borsheim.
The steel AC800PVDB feed and service barge is over 64 metres long and built for extreme conditions.
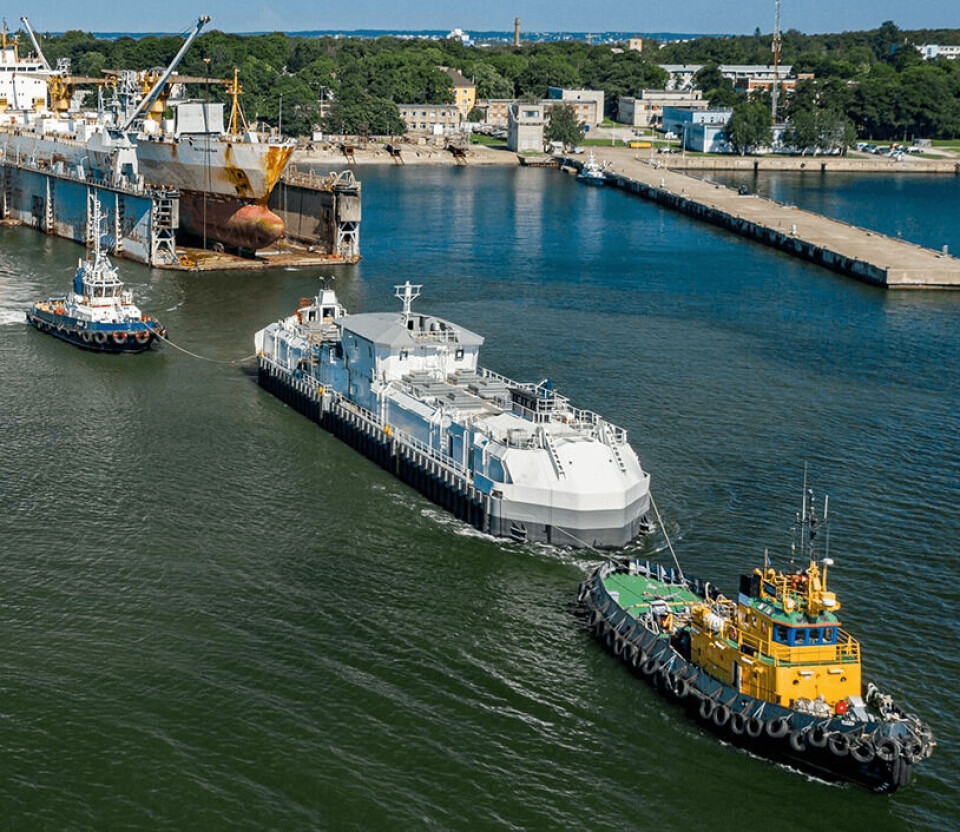
800 tonnes
It has a capacity of 800 tonnes, uses waterborne feeding technology and is dimensioned for a significant wave height of 6.5 metres, specially designed for exposed locations.
AKVA said it is also the first barge that is designed with a bottom outlet for feed hoses in order to be able to use all sides of the barge to, for example, receive feed. In addition, the barge is equipped with an integrated boat garage at the stern that can accommodate boats up to 10.5m.
“We have great respect and are very grateful that NRS/AOF trusted us to develop this feed barge that represents the extreme in many ways; with requirements to withstand very harsh weather conditions, facilitated for large load capacity operations, the environmental effects of the actual feeding technology and not least a good working environment for the crew on board,” said Hans-Øyvind Sagen, sales director Nordic in AKVA group.
Waterborne feeding
It is only the second barge to be delivered with AKVA’s waterborne feeding system, which was first presented at the world’s biggest aquaculture trade show, Aqua Nor, in Trondheim last year.
“With waterborne feeding, the barge is very quiet in operation and environmentally friendly,” said Borsheim in a press release.
AKVA said tests carried out during the development of waterborne feeding showed an energy reduction of as much as 70-90% compared with air transport.
Energy cost saving
“The low energy consumption in feeding represents a significant cost saving in generator operation - approximately NOK 200,000 in monthly savings for a conventional feeding system with 8-10 (larger Norwegian) pens,” said the project manager.
AKVA says waterborne feeding also offers almost constant feeding capacity over much longer distances than air feeding, which has a capacity of 200kg per minute over distances of up to 50m, after which AKVA says capacity decreases rapidly.
“We have measured the feeding capacity of waterborne feeding up to 600 metres, and the feeding capacity of 100kg was fairly constant even with this feeding hose length,” said Borsheim.
Semi-submersible cages
In 2018, NRS/AOF was awarded development licences from the Norway’s fisheries directorate to develop semi-submersible steel cages for salmon farming in Troms in northern Norway.
Two pens with a total capacity of 5,990 maximum allowed biomass are being built for the location Fellesholmen west of Tromsø.
The fish farm will be controlled and managed from the new feed and service barge. The pens will be ready to be populated in the summer of 2021 with the first fish produced ready for delivery to the market in 2022.