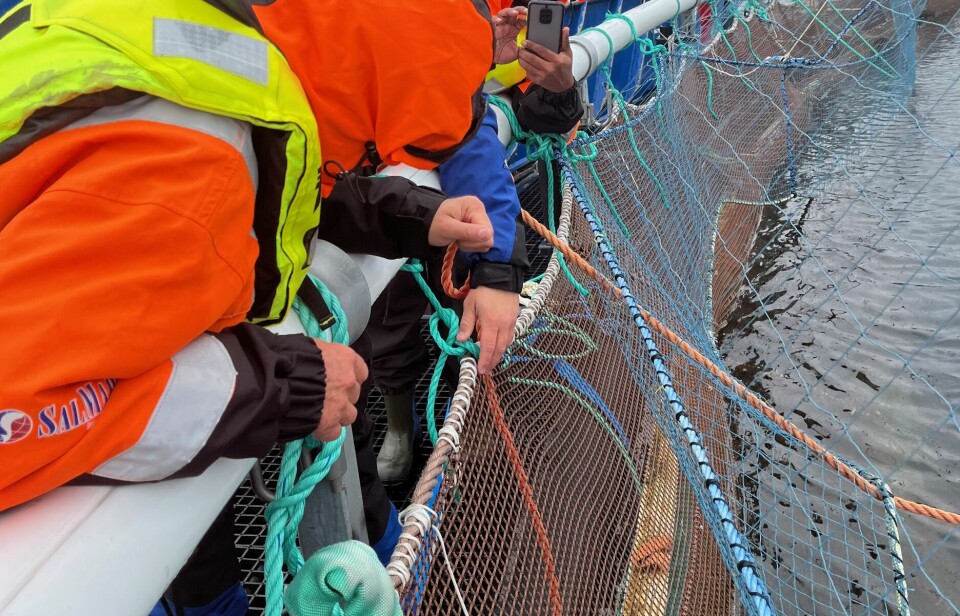
Integrated copper brings net gains for Garware and environment
The Indian company’s development of a material that was first adopted by Scottish salmon farmers is preventing pollution and winning customers
A type of fish farm net first used in Scotland is being increasingly adopted as a sustainable alternative to copper oxide-impregnated nets that can pollute the environment.
Scientists at Norway’s Institute of Marine Research (IMR) recently expressed concerns that copper anti-fouling impregnation leaching from farm nets falls to the sea floor during use and harms marine life.
“The releases of copper from the nets are of such a magnitude that we expect it to affect marine organisms,” said marine scientist Bjørn Einar Grøsvik at the launch of IMR’s annual risk report last month.
The marine researcher calculated that an impregnated net for a 160-metre circumference pen could have as much as 400 kg of copper on it. Some of the copper “bleeds” out continuously, while the largest emissions occur when the net is washed, or “flushed”, in situ.
'Up to 80kg flushed out'
“At the first flush, in the worst case, as much as 80 kg can be flushed loose,” said Grøsvik.
He was clear that flushing with a powerful water jet is the main challenge when it comes to copper emissions.
“Every time a copper-impregnated cage is flushed, there is a powerful pulse of discharge. We should avoid such pulses,” he said.
It’s a long-recognised problem, and researchers at the development department of India-based net manufacturer Garware saw a possible solution to this by developing an HDPE (High Density Polyethylene) net material in which metallic copper was built into the fibres themselves.
“We were early starters with nets in HDPE, which is a very strong material,” explained Pål Korneliussen, Garware’s country manager in Norway. “The fibres are much thicker than nylon and HDPE does not absorb water, so the nets withstand washing and harsh treatment. Thus, the strength is retained after many years in the sea.
“The first HDPE bags had thick thread with high stiffness, but now they match the thread thickness of impregnated nylon.”
Metallic copper
Korneliussen said Garware first got the idea to extrude metallic copper into its HDPE nets in 2016.
“Metallic copper is much less toxic than copper oxide and is thus less effective against growth, but pure copper still has a good effect. Our idea was to lock the copper into the plastic fibres so that it cannot fall off and sink to the seabed and contaminate the sediments,” he said.

This was not as simple as it sounds as the metal is an impurity that weakens the strength of the HDPE thread.
“After much trial and error, our researchers managed to make a strong material in HDPE with a proportion of copper inside. We could make net bags, ropes, and lice skirts out of this.”
The material was used the make Garware’s V2 nets, first tested at sea in Scotland in 2018. Korneliussen said the results were very promising, with reduced growth and less need for washing.
Easier to clean
“It was also clear that the biofouling was less stuck and was easier to wash off in the sea. Less washing means less disturbance and impurities inside the cage and better conditions for the fish. Not least, this is important for gill health.”
Similar results were seen in Canada, but it was the Scottish customers who showed the most interest at the start.
Around the same time, the company started marketing the V2 nets in Norway.
Garware’s major breakthrough in Norway came after the country’s second largest salmon farmer, SalMar, tested two V2 nets in the summer of 2019. The company saw a significant reduction in washing in sea compared to ordinary HDPE, with a corresponding reduction in washing costs.
“SalMar were so satisfied that they have so far bought over 150 V2 nets from Garware through our partner Selstad. The nets are in the sea from Smøla to Mehamn. As far as we understand, they will continue to replace their old nets with V2,” said Korneliussen.
Saving on washing costs
The nets are not cheap as copper is expensive, but SalMar offsets the extra expense in reduced washing costs, according to Korneliussen.
“On average, their washing is reduced by approximately 40% compared to normal HDPE nets. This constitutes a significant saving in costs.”
According to Korneliussen, the service stations that have had the V2 nets for service report significantly less need for repairs of holes, etc., than what they see in traditional nylon nets.
“There is always some mesh breakage and accidents happen, of course, but on average they say that HDPE needs around a third of the work of a nylon net. It also means big savings for the farmers.”
He praised the farmers’ willingness to be innovative.
“It is what drives the world forward. In total, we have now delivered approximately 400 of these nets around all salmon regions in the world, over half to Norway.”