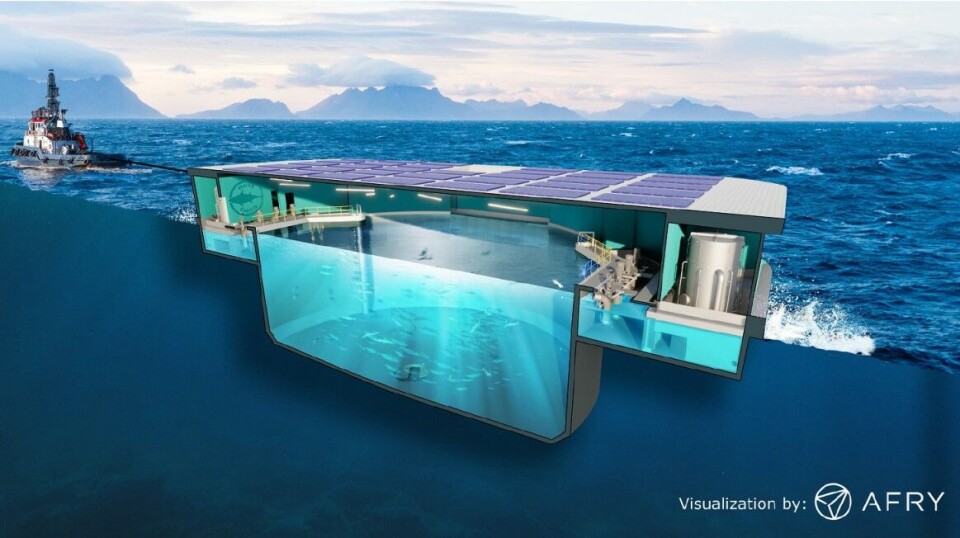
Floating RAS ‘can be aquaculture’s answer to climate change’
Next Tuna gives details of system claimed to solve sea challenges but cost less than land-based facilities
A German company has revealed details of its plans for a climate change-proof floating recirculating aquaculture system (RAS) which it says can solve the problems faced by open net pen fish farmers and will be cheaper than land-based RAS facilities.
Frankfurt-based Next Tuna has designed the RASxFloater in collaboration with Norwegian company Seafarming Systems, a specialist in floating closed and semi-closed containment that jointly developed the Aquatraz semi-closed system used by salmon farmer Midt-Norsk Havbruk (now part of SalMar).
The companies filed for intellectual property protection with the Norwegian patent authorities before Next Tuna presented the design at the Aquaculture Europe conference in Vienna last week.
In a presentation at the conference, Next Tuna co-founder Paul-Daniel Sindilariu said that the RASxFloater concept was developed to grow Atlantic blue fin tuna juveniles but was suitable for growing a wide range of fish, such as salmon post-smolts, barramundi, kingfish, and tuna.
Insulated steel tank
The design is comparable to a 30-metre diameter, 10m deep net pen (7,000 m³), but instead of a net that keeps the fish, the RASxFloater has a fish tank made of insulated steel. The RAS treatment infrastructure is housed on the same floating structure.
The concept is designed to be used closed to shore in sheltered areas with waves of no more than 1 metre, but the designers are looking at solutions to enable it to be used in more exposed sites.
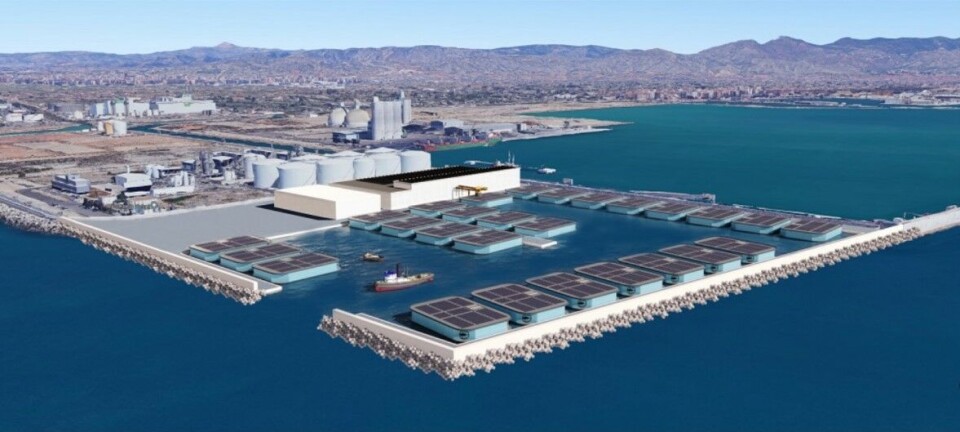
The RASxFloater has two operational modes: a production mode where the system is connected to a harbour dock, or moored in a sheltered area and receives all essential supplies from land or barge; and a delivery mode where the system is disconnected from land supplies and pulled out of the sheltered/harbour area by tug into the open sea.
Because the system is fully enclosed, effluent can be
treated on land or on a barge, and because water pre-treatment is incorporated,
the RASxFloater can be used in areas where water quality isn’t good enough for
net pen aquaculture, said Sindilariu.
Insulation of the steel walls will also enable cold water fish to be grown in warm water and vice versa, and the insulation will also serve to mute the sound of waves hitting the structure.
Climate threat
“We all know that climate change is a threat to aquaculture, especially when we look into open net pen aquaculture. We see that events of extreme heatwaves are going to be more frequent, we’re going to have more storms, more flooding, a more unsafe environment for open production in aquaculture,” said Sindilariu. “These events lead to adverse production environments like algae blooms, water pollution that we cannot keep away from our fish, jellyfish invasions.
“On top of that we have the impact of farming to the surrounding environment, and the feedback loop to the farming environment [from fish faeces]. This then adds to image loss for aquaculture, and we see restrictions in licensing, and even public penalties like the tax in Norway or the reduction of the number of licences in Canada. These are all effects that are working against open net pen aquaculture, so we must have different approaches for an efficient, climate-resilient form of aquaculture production.”
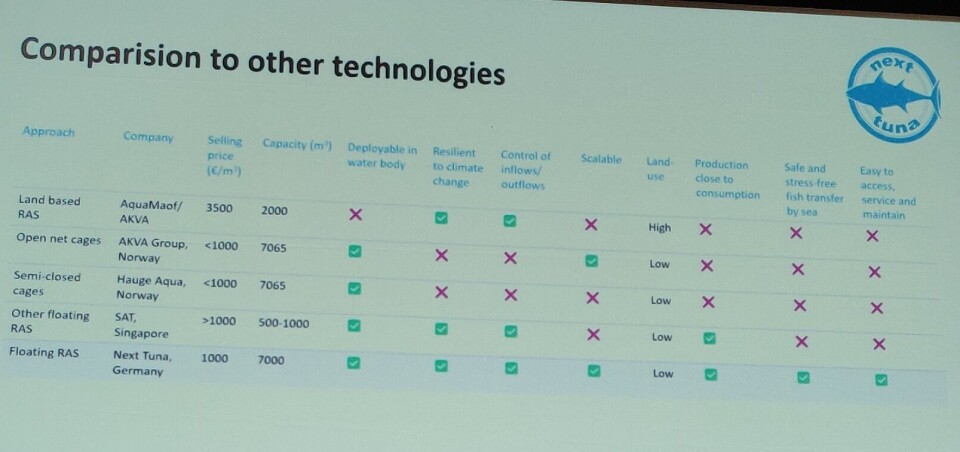
The RASxFloater would be cheaper than a land-based RAS, costing a projected €1,000 per cubic metre instead of €3,500 per m³, according to a slide shown during the presentation.
“Compared to a land-based RAS we can reduce the construction costs. First of all, there is no land needed, we don’t need to do any groundworks, we don’t need any concrete,” explained Sindilariu.
“The fact that the inside and outside water levels are virtually the same means we don’t have a big pressure difference between inside and outside so the wall thickness can be much thinner and, since it’s floating, it is easy to service because as soon as we pump the water out the system starts floating (higher) and is accessible inside and outside for service and maintenance.
“It’s a modular set up, so we can add modules to the facility as we increase our scope.”
Clear advantages
He added: “Compared to land-based, open net cages, semi-closed cages, other floating systems on barges, we can see that for most of the systems we have clear advantages, especially when it comes to the price of building the system, flexibility, resilience to climate change.
“We see this floating RAS as a future for marine aquaculture, especially as it is climate change resilient. We are not dependent on the increasingly fluctuating environment, we can increase the production capacity, it is suitable for aquaculture at the worst sites.
“Furthermore, it’s site-independent, you can produce close to the customer, for instance; we are in control of water parameters, as in land-based RAS systems; we reduce the stress from transport because the system is moveable; we avoid disease and parasites. Additionally, we don’t have any pollution to the system because the system is completely closed; no effluent, because it is treated on land; no escapees; and with the RAS system we can treat the water as much as necessary.”