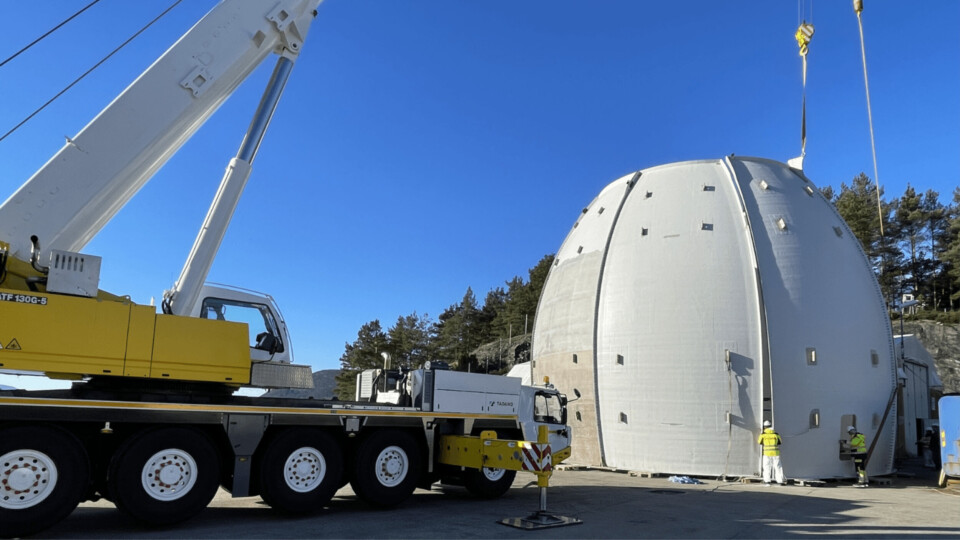
‘Egg’ salmon farm taking shape in Norway
The commercial prototype of a novel salmon farming enclosure, the Egg, is nearing completion in Norway ahead of a handover to customer Hauge Aqua during the spring.
The first Egg – known as the MiniEgg – will be 21 metres high and 15 metres in diameter and have a farming volume of 1,850 cubic metres. This is only a tenth of the planned volume of the full production version but paves the way for the main project’s 44-metre-high Eggs.
Fabricator Herde Kompositt, in Ølve, on Norway’s famous Hardangerfjord, is building the Egg, which has a composite shell. It is scheduled to be in the water and ready to receive fish by May.
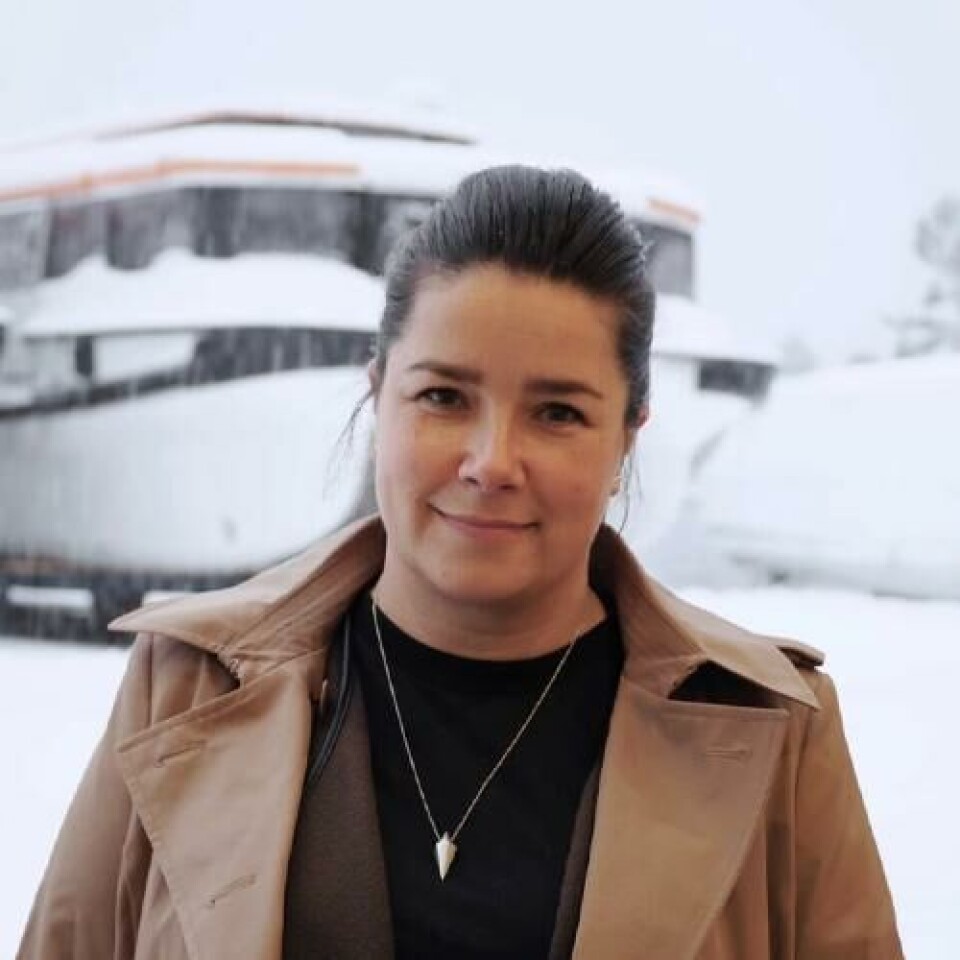
Working intensively
Herde Kompositt development manager Kristine Moldenhauer Biseth told Fish Farming Expert’s Norwegian sister publication, Kyst.no, that the company is working intensively on the project.
“Much of the work is still being done indoors to complete the large parts that will become the Egg. We have started to build parts of the Egg on the quay. This is module C which is the ‘main part’ that the fish will be in,” she said.
Despite the fact that this first version is called the MiniEgg, there is nothing mini about the parts of the Egg that the company is now putting together. The concept is an egg-shaped closed fish farm with flow-through plant, where the water is pumped in from the bottom, set in motion and filtered before it is released.
Post-smolts
The MiniEgg is expected to be used for growing post-smolts to one kilo before transfer to net pens and can also be used for broodstock in the last part of the sea phase.
Most of the equipment work is done by Herde Kompositt’s own employees, but there are some subcontractors who are installing in parallel with them now.
“Several subcontractors will be involved in commissioning and testing before the Egg is to be delivered,” said Moldenhauer Biseth.
The number of employees involved in the project is increasing as the delivery date draws closer.
“When we started operations on April 1 last year, we had 49 employees. As of today, we have 70 employees, and we have a need for even more.”
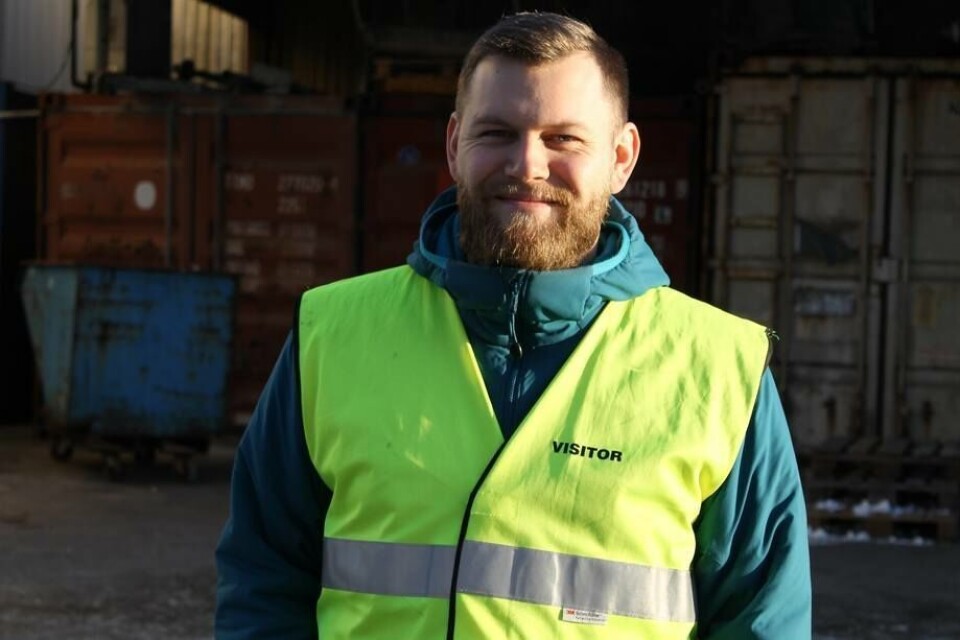
A plan coming together
Jens Martin Gjærum is a construction follow-up engineer for Hauge Aqua and has been given the task of following up the construction of the Egg at Herde Kompositt. He said that it is pleasing to see that things that have been on the computer and in calculations are finally taking proper shape.
“That’s when you really see how big this project actually is. Of course, there are a few arms and legs to get everything fixed that needs to be fixed, but that’s part of it,” he said.
Gjærum said that all large sections - the dome at the top, the floating collar, the main part of the Egg shell, and the bottom section – have been fabricated.
The remaining activities now will be the assembly of the four main sections, as well as some installation of equipment and connection of the electrical and automation system. The final finish will be hatches, doors, strainers and filters. Finally, a test run is carried out in a floating position in the fjord outside Ølve.
“In parallel, we are working to ensure that everything is ready for reception at the site,” said Gjærum.