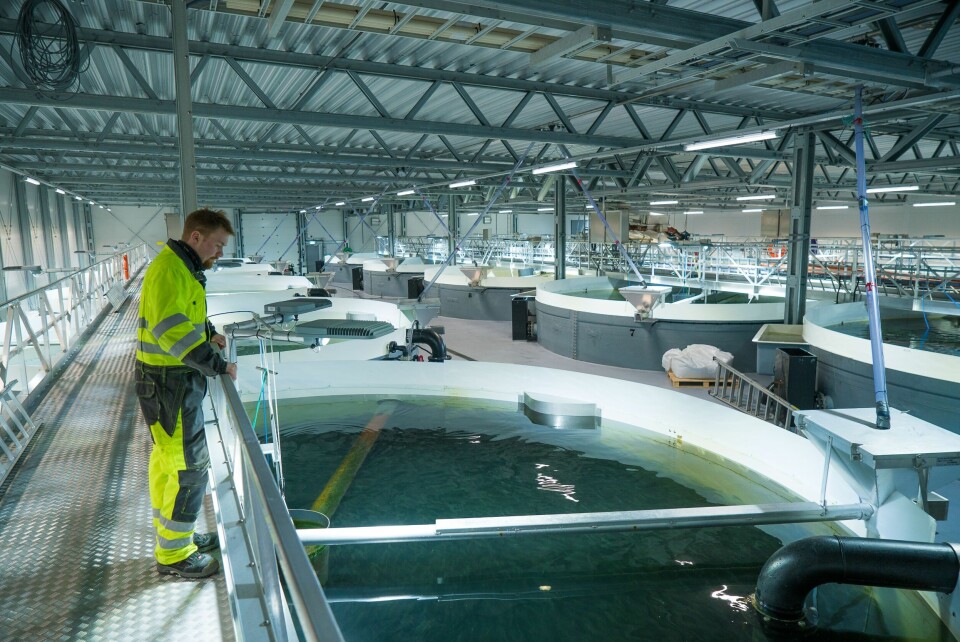
RAS takes the heat off smolt producer
Changing over to a recirculating aquaculture system (RAS) brought a bonus for Norwegian salmon farmer Bremnes Seashore during the recent hot, dry weather.
While some flow-through hatcheries were practically out of freshwater, the much smaller water requirements of a RAS meant the company never sweated over its supply in the sunshine.
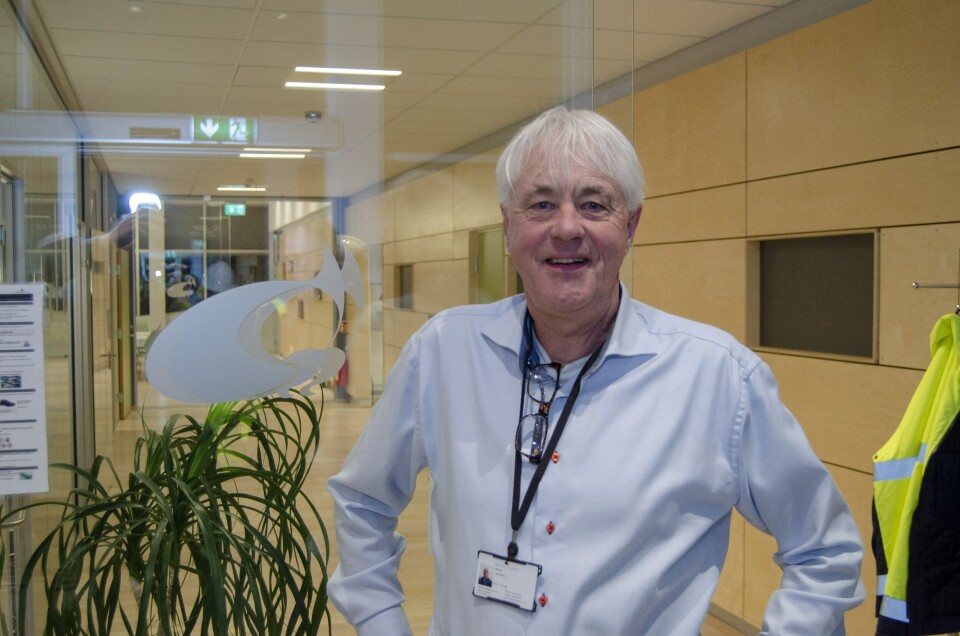
“With the old plant with no RAS and 150 tonnes of production, we would have had to take drastic measures, otherwise there would have been little freshwater left,” said Øyvind Haraldseid, in charge of the plant at Trovåg, north of Bergen. “Instead, we now produce several times more biomass and use less water than ever.”
Freshwater basin
A survey of the freshwater basin used by the hatchery recently showed that the level had dropped by just one metre of a total of 2.6 metres available, despite an extremely dry summer.
“It feels good not to consume that much fresh water, water is a limited resource. RAS is the future of fish farming, it also has other benefits,” says Haraldseid.
The first of a planned four RAS halls has been in operation for two years. The second hall has been in operation for half a year, and the third and fourth halls are under construction.
“With the RAS, we can keep higher temperatures in the plant in winter. Salmon on land are also not bothered by parasites. We plan to keep the fish until they are half a kilo,” said Haraldseid.
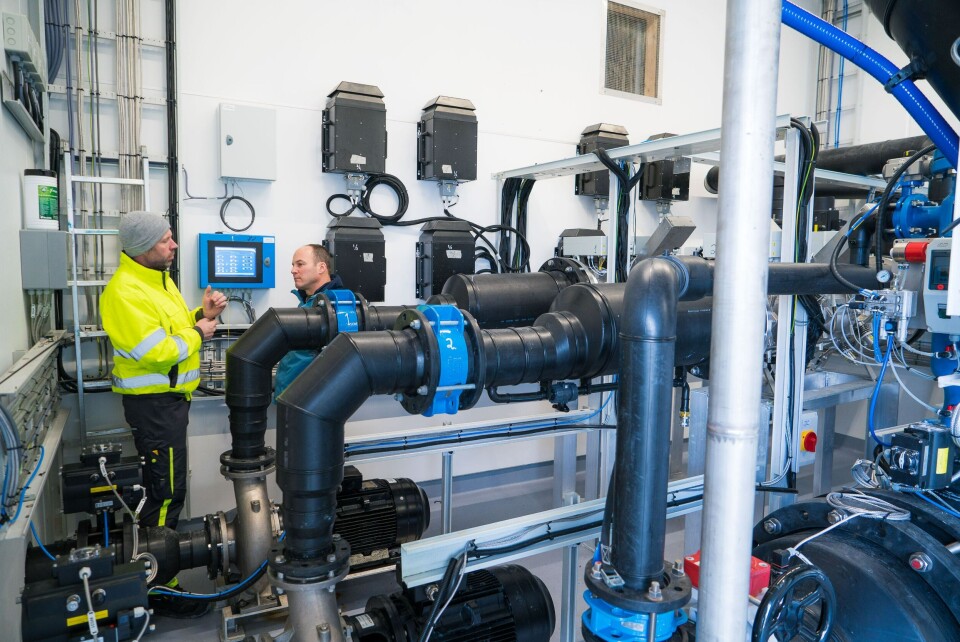
3,500 tonnes of smolts
Bremnes Seashore plans to gradually increase production to approximately 3,500 tonnes of biomass, which is expected to occur in about two to three years.
“On normal flow-through, it would be impossible to produce these quantities on land, at least here at Trovåg,” said Haraldseid. “The RAS consumes little water per kilo of fish; we have already reduced it by 95% and it will go further down. In combination with the sea water we pump in from 75 metres deep we can let the salmon grow on. In the future I reckon the fish will spend one year at sea, and perhaps even less,” said Haraldseid.
In the long run, it is estimated the plant will produce eight generations per year.
By expanding its RAS and the size of its smolts, Bremnes Seashore will be able to increase production at its sea sites because fish that go in at 500 grams will reach harvest weight sooner.
25 times more biomass
Until two years ago, the company had permission to produce 10 million smolts and 10 mill fry per year, limited to 2,850 tonnes, at Trovåg, but has since been given permission for 6,000 tonnes per year at the site if it wants to expand that much.
“In all we expect to increase the biomass on land by a factor of 25. This will use less than half of the water we now have available,” said Haraldseid.
The RAS plants are built as separate units. Hatchery and start feeding are also closed systems. All the equipment is supplied by Sterner, which has also delivered sludge treatment facilities, and has now developed a modular RAS after producing a steady supply of RAS for different customers.
A RAS in six months
“Customers see time as money, we now deliver a module in six months,” said Kim David Lid at Sterner. “If you already have a plant, we prefer to look at it before we get started, as a module is not always the best choice.” He said the firm’s customers also have preference, with some wanting to use ozone while others don’t.
“RAS is not rocket science, but never easy,” said Lid. “Some like to build it on their own. It may work if you have experience and expertise in hydraulics, water treatment and biocultures. Working with a fixed concept like the RAS modules has provided us new knowledge, and in a few weeks we’ll deliver our seventh RAS module. The modules are readily designed in different sizes.”
He said the most common mistake is incorrectly calculating the hydraulics, as large amounts of water and large-dimension pipes are needed.
“A Coke bottle looks nice on the table, but if you turn it upside down you will see that it is not designed for quick emptying. These are the things that must work in hydraulics,” said Lid.