
Havfarm’s 11-tonne nets take shape in India
At a large factory in the Indian countryside this week, the first of six nets to be used on the Havfarm development project in Norway is being finished. There are several things that make the net special.
Netting, technical textiles and rope manufacturer Garware Technical Fibres has its largest factory located a good five hours by car east of Mumbai, a city of 20 million people. Here you will find the much smaller city of Wai, home to about 50,000 people. By far the largest employer is Garware, which provides jobs for around 5,000 of them.
And the absolute biggest project at the moment is the production of the six cages that will go to the Havfarm, the ship-shaped salmon farm being built for Norwegian salmon farmer Nordlaks.
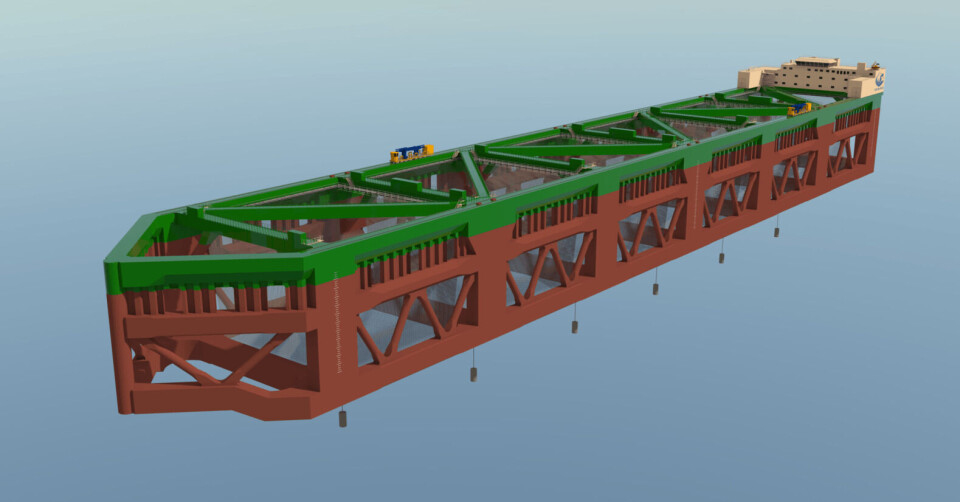
47 x 47 metres
Garware produces for the Norwegian supplier Selstad, and when Fish Farming Expert’s Norwegian sister site Kyst.no visits, both Steinar Hansen, head of fish farming equipment at Selstad’s department in Svolvær, and operating technician Torstein Solberg are there to ensure the production goes according to plan.
“It is the first of six nets for the Havfarm that we are putting together now. A lot is new and special, so it will probably take an extra-long time with this one, I think we will spend about ten days on it. The other nets will probably go much faster,” says Hansen.
Each of the nets will have a dimension of 47 x 47 metres, and will be straight-sided for 35 metres before angling into an inverted pyramid shape at the base. Maximum depth will be 56 metres and the volume of water in each cage will be 70,000 cubic metres.
“The weight of each net will be about 11 tonnes, including rope. A regular farm net usually weighs between one and eight tonnes,” says Hansen.
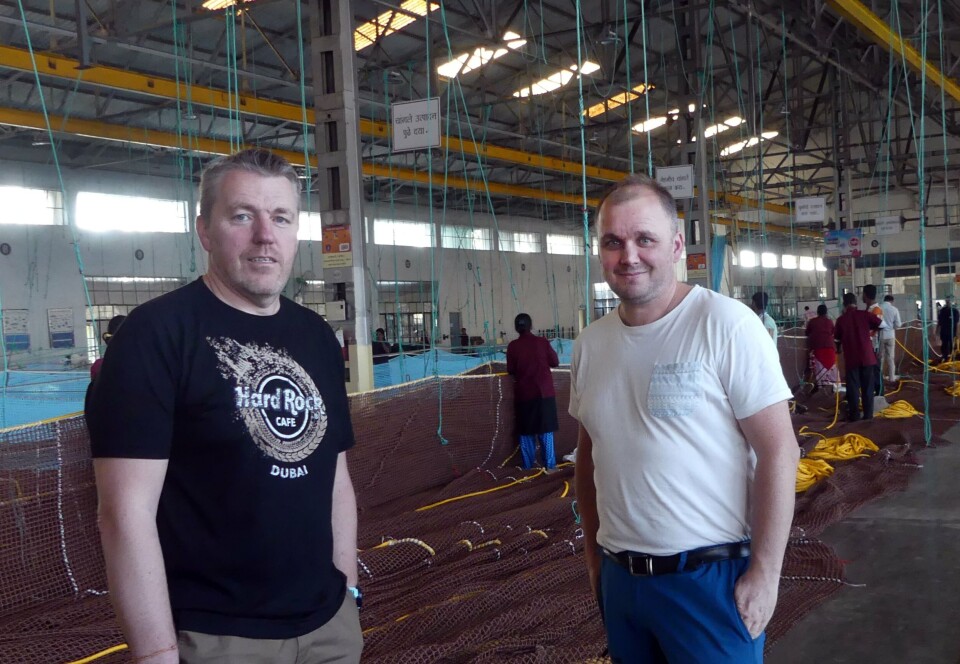
Relatively escape-proof
Nordlaks stated in the application for development licences for the Havfarm that it sent to Norway’s Directorate of Fisheries that each Havfarm should have a capacity of 10,000 tonnes of biomass. This means that there may be just under 1,700 tonnes of fish in each cage at most.
When it granted the licences, the Directorate of Fisheries stated that, with some reservations about the correct calculations, it believes that the Havfarm will be able to operate as relatively escape-proof.
Selstad’s Hansen agrees.
“The netting, also made here at Garware’s factory, is made of HDPE (high density polyethylene) which makes the net much stronger than traditional nylon nets. And that’s important, because this is not a net that can easily be taken up after nine months. This should be able to stand at sea for ten years or more,” he explains.
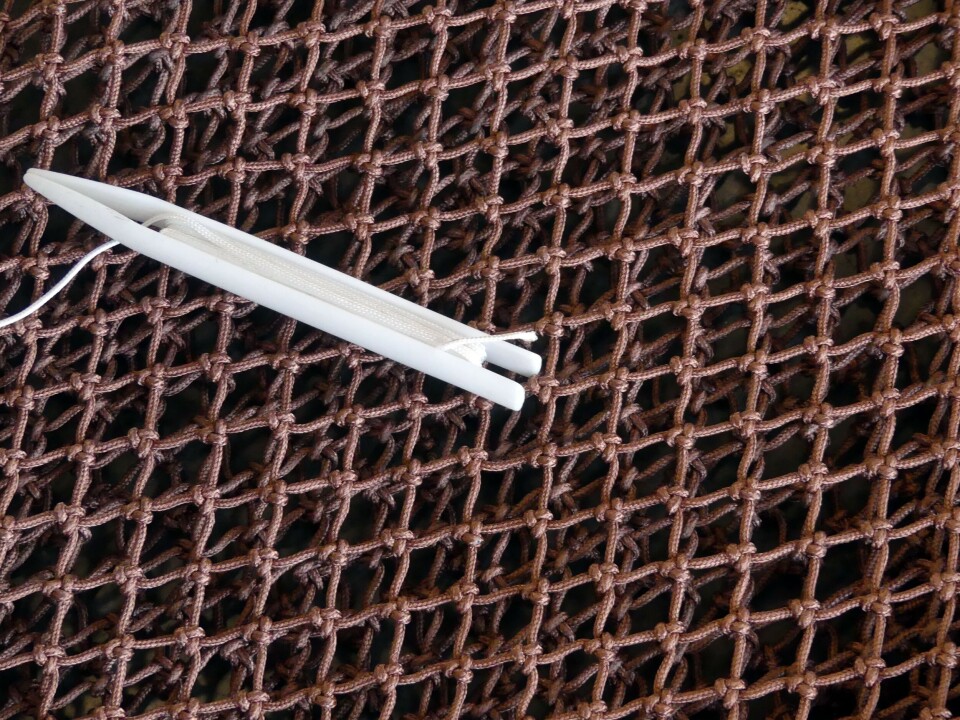
Copper microparticles
The fibres in the net are also coated with copper microparticles.
“This is a so-called third-generation V2 net. With the copper inlay, you get an anti-fouling effect, without the problems of spot emissions of copper that traditional copper impregnation can give,” Hansen says.
The copper will leach out over time, but slowly and in ion form, so it shouldn’t noticeably affect the natural concentration of copper in seawater.
New technology
Hansen says that this technology is so newly developed that it was not included in the original planning of the net.
“This summer, however, a decision was made to go for this.”
The Selstad man won’t say what his company charges for such a giant cage, but the cost of developing it has not been small.
“There is a lot of thought and development work behind it, all the details are carefully thought out. But it has been a fun project,” he emphasises.
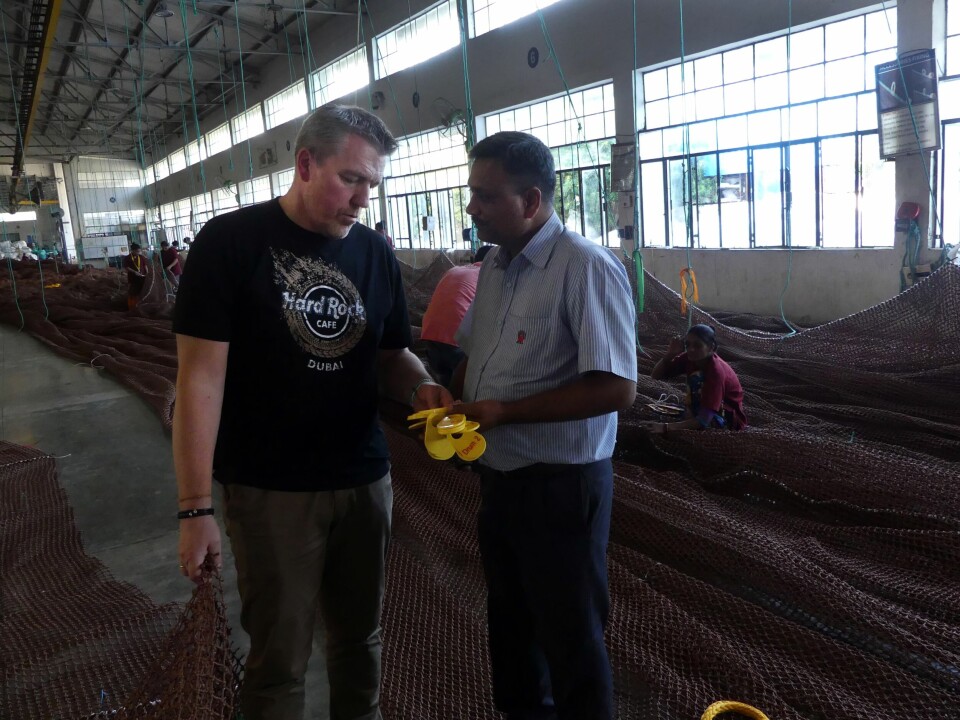
High-level crafts
Unlike a nylon net, HDPE does not shrink when it reaches the sea, so everything must be 100% on target.
Hansen compliments the work Garware’s staff are doing.
“These are high-level crafts that they perform here. After all, they have 15 years of experience in making purse nets in Norway, so they know their subject.”
When all the six nets are finished after New Year, they will be packed in containers and shipped for about 75 days to Norway, where the first Havfarm will be stationed at the outer Hadseløya site in Vesterålen in Nordland.
The first fish are scheduled to be placed in the Havfarm nets in summer next year.