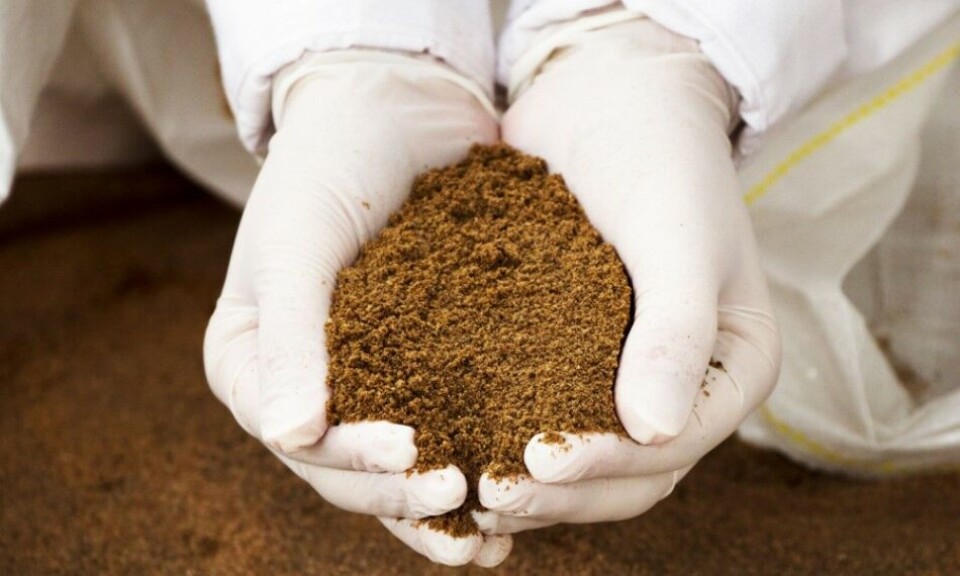
Insect meal additive boosted shrimp growth by 17%
A feed trial conducted by aquaculture researchers attached to Kasetsart University in Thailand returned impressive results for shrimp fed a diet that included an insect-based feed additive derived through a process said to yield 10 times as much as traditional black soldier fly (BSF) farming.
Pacific white shrimp (Litopenaeus vannamai) given feed containing a 2% ratio of the additive from Full Circle Biotechnology increased in weight by an average of 17% more than shrimp fed a control diet in the 45-day trial.
The feed conversion ratio (FCR) of the shrimp given the Full Circle additive was also 14% better than the shrimp fed the control diet. There was no shortfall in the quality of the shrimp on the Full Circle diet, either in percentage of protein or health of the shrimp.
The control diet contained 21.5% high protein soybean meal, whereas the experimental diet contained 20% high protein soy and 2% of the Full Circle product.
Carbon footprint
Thailand-based Full Circle Biotechnology claims its product has a carbon footprint 100 times lower than soymeal and almost 700 times lower than fishmeal, and hopes the feed trial will pave the way for greater substitution of soy and fishmeal in aquaculture diets.
In May, Full Circle’s British founder and managing director Felix Collins told aquaculture medium The Fish Site that the company is developing what it calls its Black Box, a fully automated facility that can produce 6,000 tonnes of Full Circle protein per year using just 1,500m² of space.
“This comes with many challenges, but the most significant for us is uniformity and consistency across borders. The Black Box is designed strictly to EU standards, but every new country still requires a thorough regulatory analysis and with some clients, their governments are slow to comment on BSF at all, let alone completely new technologies,” Collins told the website.
10 times more product
The company uses agricultural waste that is upcycled with microbes and mixed with BSF larvae before being processed further. It says its proprietary, patent-pending process means that every 100kg of substrate used generates 24kg of product, almost 10 times more than most traditional BSF yields of 2.5kg.
Its process enables it to use a wide range of ingredients.
“We can and do use a smorgasbord of different substrates and in most cases we leave this up to our clients,” Collins told The Fish Site. “We can achieve a crazy protein range, from 10 to 70%, so it depends on the exact demand from customers, as well as their location. With one very well-known customer we’re using a mixture of abattoir by-product and by-product from the cassava industry.”
The company has venture capital backing from Norwegian impact accelerator Katapult, and says it is developing a footprint in the Norwegian salmon industry.