“Three technologies seek to reduce costs in the salmon farming industry”
By Carlos Bohle Salas
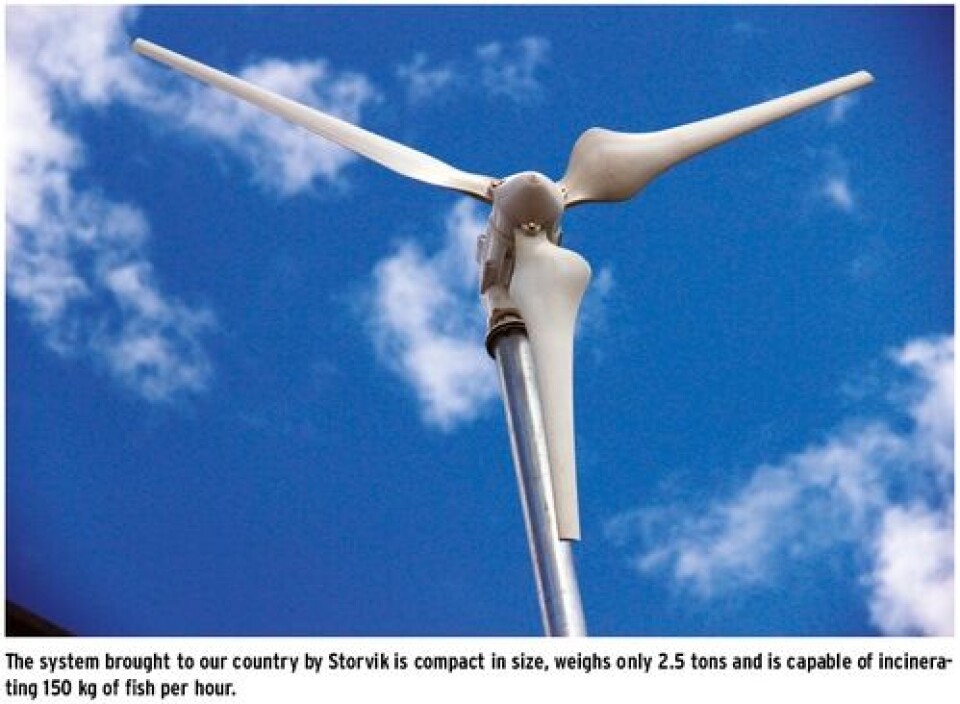
The constant implementation and development of innovative technology have been frequent topics in the salmon industry over the years. Nowadays, the situation is not different and Chile is constantly trying new ways to improve the profitability of the business, using incinerators, renewable energy sources and new forms of transportation and containment of fish, that represent a promising future in the development of the industry.
Storvik Chile with its fish incinerator, Luxmeter Energy through their wind systems for fish farm pontoons, and Asenav with SAAM, introducing their new containers called tanktainers, are three companies behind the launching and marketing of new technologies for the Chilean salmon farming industry. The operation of the equipment mentioned above will be described individually in this article.
Efficient and profitable equipment with cutting edge technology New incinerator would allow savings of 25-30 percent
In order to reduce the costs associated with disposing the mortality generated in farms and hatcheries, the aquaculture equipment supplying company, Storvik SA, has begun to introduce in Chile biomass incinerators of British origin. These incinerators could save between 25 and 30 percent of the value currently intended for silage waste.
The device, designed by the British company AddField, weighs 2,5 tons and requires about 35-45 liters of gas to incinerate 150 kg of fish, a process that takes about an hour. During that time, it converts biomass into inert ash - which does not need to be taken to a dumo or landfill - the weight of which is comparable to the 3 percent of the initial dry weight.
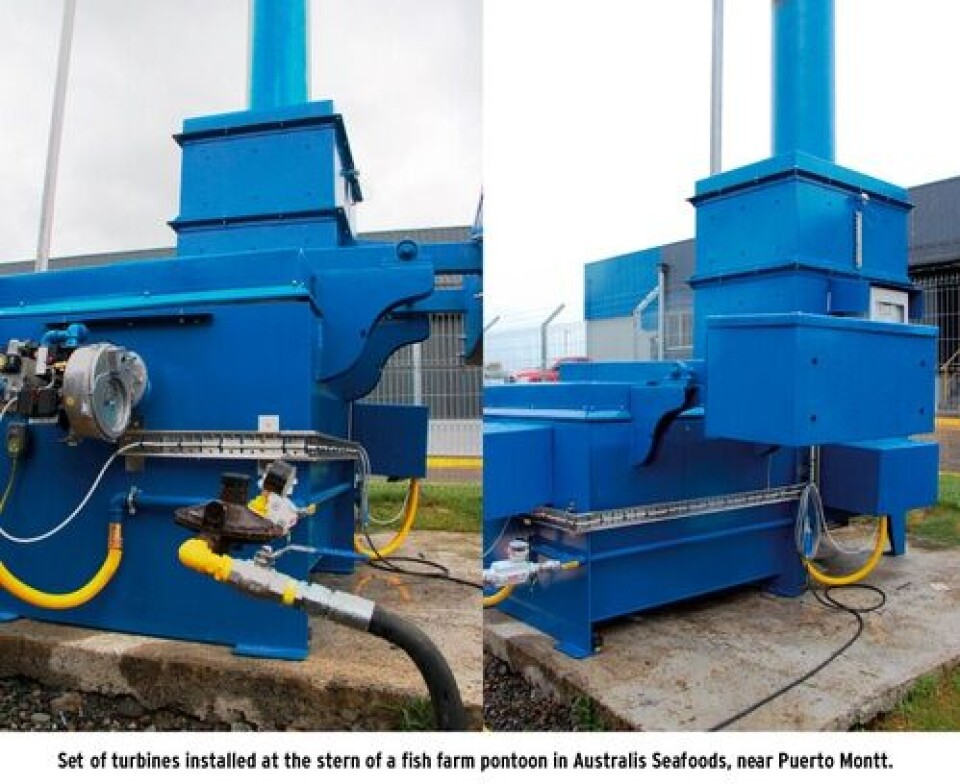
The commercial manager at Storvik Chile, Juan Pablo Barrales, explains that this equipment was brought to our country as a response to the rising costs associated with mortality in the national salmon industry. “The value of lading has increased, as well as costs of acid and silage systems. Moreover, in this case the removal of waste is reduced substantially, with only 3 percent of the dry weight added to the device initially,” he says, adding that, although is difficult to quantify, the improvements in health, biosecurity and operation are also significant.
This first incineration project is being conducted in conjunction with Abastible, who are the owners of this first unit and also have the know-how for the development of this technology, with a significant range of equipment installed from the VII to XIIth region in Chile. He adds that the energy consumption of this equipment is extremely efficient because it operates on heat pulses, instead of burning biomass with a steady flame. This incinerator operates on Liquefied Propane Gas (LPG). It complies with all the regulations associated with its use. For example, it provides heat insulation which prevents outward dissipation.
One of the standard requirements is to incinerate all the resulting particles. To achieve this, the device has two chambers. Biomass is incinerated in one while gases resulting from the first process are burnt in the other. Therefore, “this device does not emit smoke or odours” Barrales explains, pointing out that the regulations (Decree No. 45 on incineration and conicineration) in our country determine that the primary chamber should be operated at 850°C and the secondary chamber at 1,100° C for a period of 2 seconds.
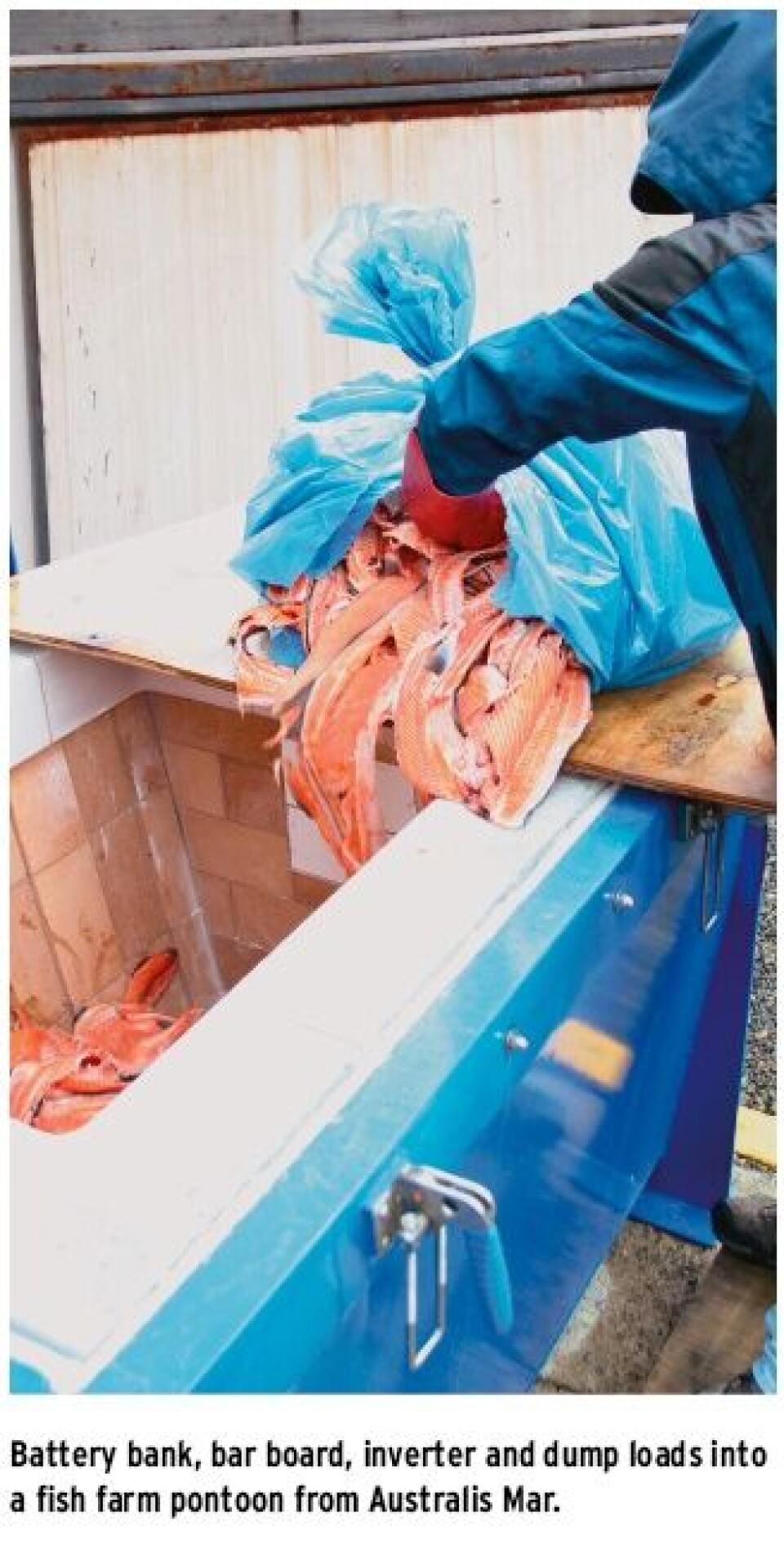
According to the description by the general manager of Storvik Chile, there are other incinerators operated by Chilean salmon farming companies, available at a similar price but with a different level of efficiency. “There are a few, for example, designed to incinerate 200Kg/hour, that consume about four times more fuel than ours. In addition, they weigh about 6 tons and require much larger platforms, both because of their weight and in order to support the greater number of collection tanks with the gas they require”, Juan Pablo Barrales says.
The incinerator is to be installed shortly in cooperation with Abastible at a fish farm near Puerto Montt, so as to verify the qualities described in the equipment catalogue on-site. Wind turbines Silent technology that powers habitability On the subject of cost reduction at salmonid farming facilities, the fish farm pontoons with wind systems present a clearly visible option, because of the turbines erected on structures that, in addition to supporting the power generation, also provide them with a unique shape.
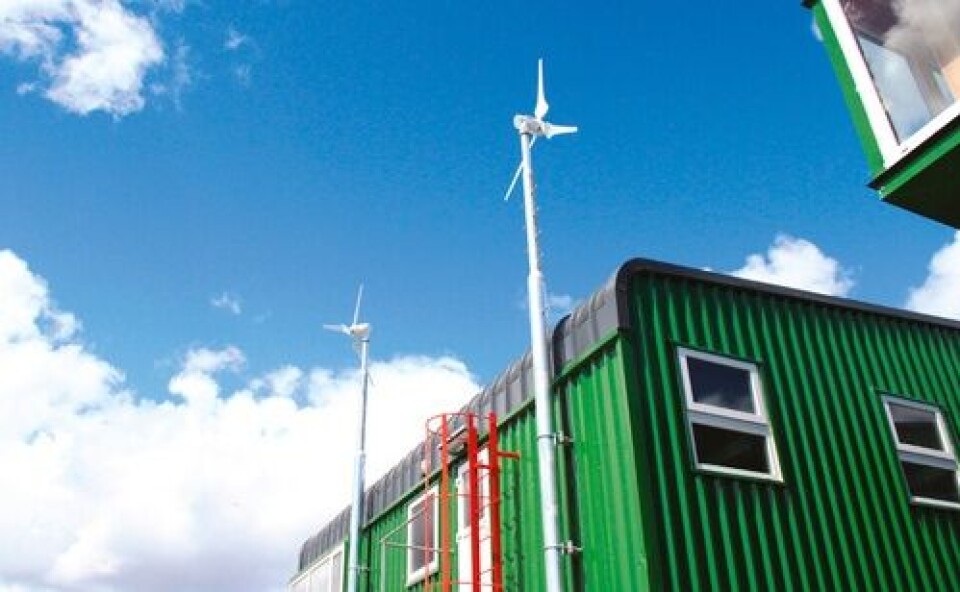
The Luxmeter Energy company, dedicated to delivering energy solutions in southern Chile, has developed wind and solar equipment to supply renewable electricity at various salmon farming facilities. The Chilean salmon industry is coming to rely slowly, but surely, on these environment friendly systems.
With several projects, Luxmeter has laid the groundwork for the implementation of wind systems at fish farm pontoons located in southern Chile. In this issue we will describe a system that uses 5kW/h wind turbines, installed at seven fish farm pontoons of Australis Mar, located in the regions of Los Lagos and Aysén. This equipment can provide the same power as that of 12 hours of diesel usage, involving great savings and resulting in peace and quiet at the facilities during the night.
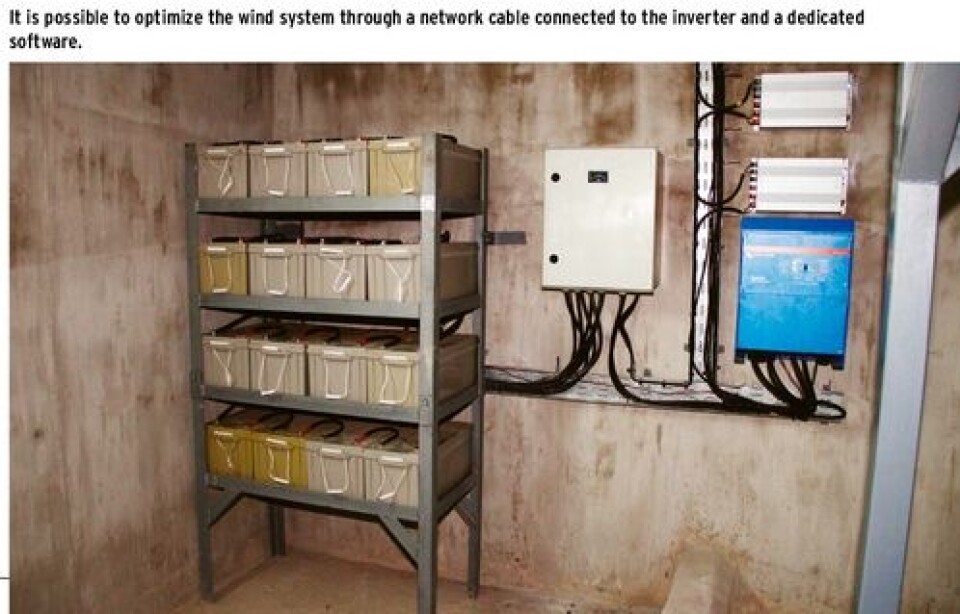
Australis Mar is one of the salmon farming companies that has installed wind turbines in their Puerto Montt and Aysén facilities, which have adopted the name “efficient fish farm pontoon”. Each of these has two wind turbines mounted on its stern, which generate approximately 5kW/h, totaling around 120kW per day, for a system developed to cover the entire electricity demand associated with staff habitability (interior and exterior lighting , computers, lift pumps, televisions, etc.).
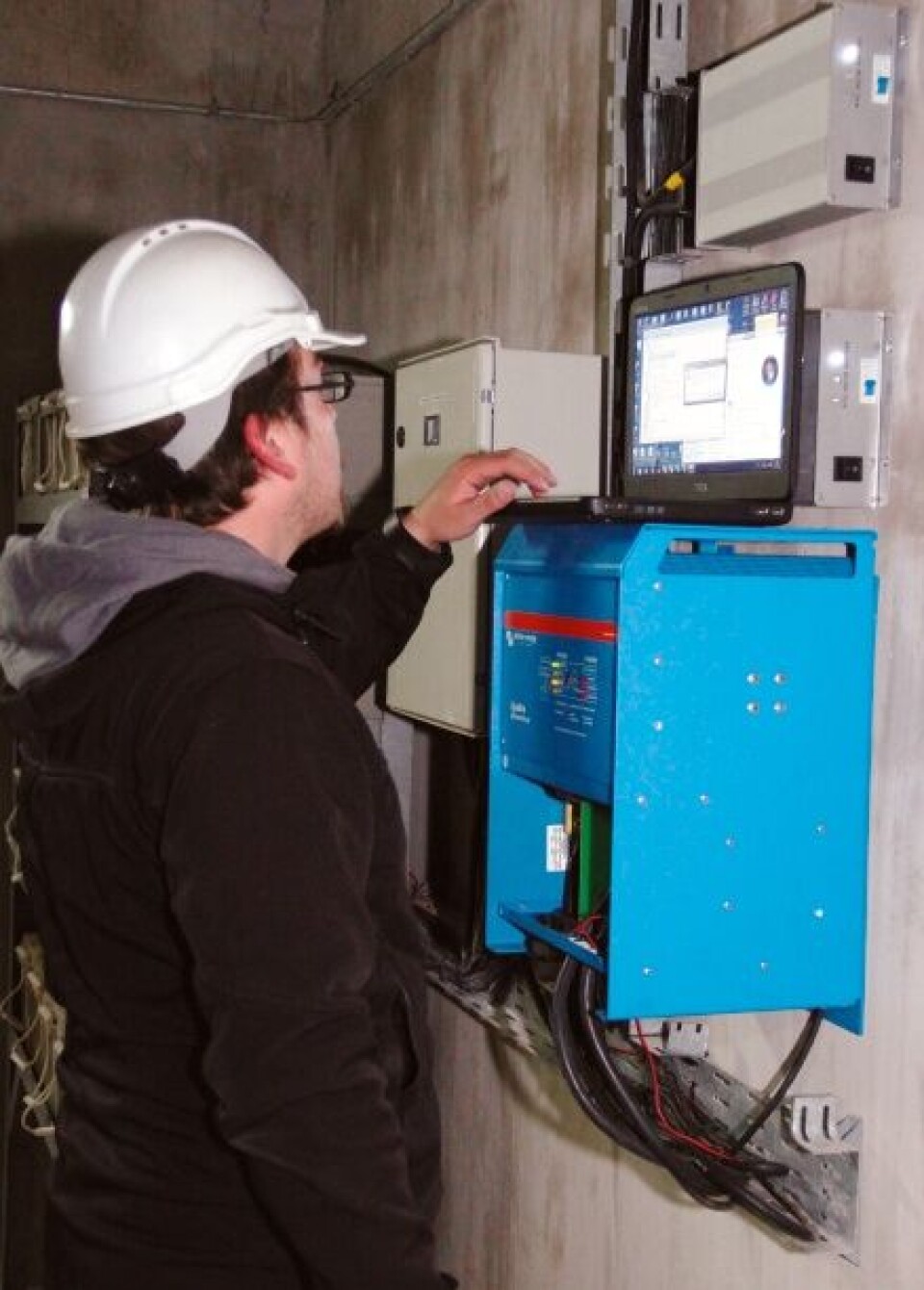
This wind system, called LX T4000, has so far complied with the promise of delivering innovative, efficient and low cost energy, and has satisfied all the people who live and work on these fish farm pontoons.
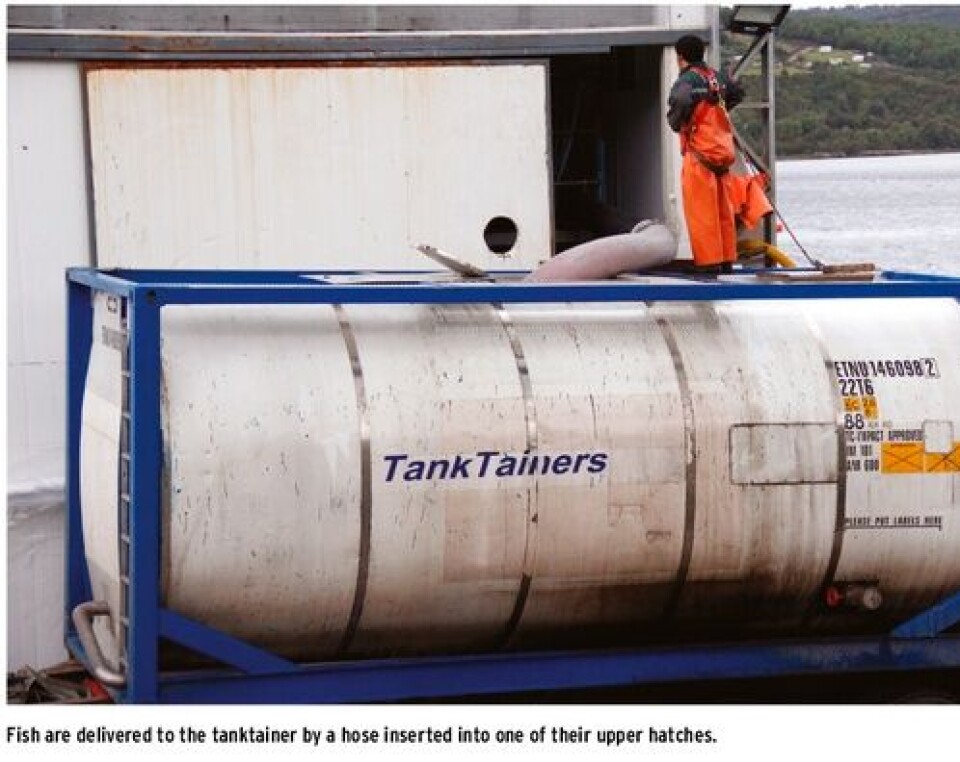
The first pontoon with wind power was installed in November 2011 in the Aysén region. The first three systems were installed at sea facilities, which caused some initial complications that Luxmeter took care of. The other devices were installed in the shipyard, allowing the incorporation of this new system in all the new facilities.
At present, Australis Mar is saving an estimated total of 2200 liters of diesel per month for every site that is equipped with wind turbines, although their future savings projections are more ambitious. The company has contacted Luxmeter to substitute the lighting at all its sites with LED lamps, which will improve energy efficiency even futher. The autonomy required per facility is 12h a day, however, in extreme circumstances the system is capable of providing power to the fish farm pontoon for at least three days, without needing the support of a generator. The daily monitoring required by this equipment consists of checking the hours of usage and the fuel consumption.
The turbines have performed excellently in the abrasive environment where these houseboats are located. The wind speed is a complicating factor in Aysén, since centres can easily record wind gusts of more than 140km/h in winter. For this reason Luxmeter had to change the design of the turbines opting for tailless models, devices much more resistant to these weather conditions. The diesel-based generator maintenance has been decreased because it is now used more moderately, with a resulting decrease in fuel transport.
Another aspect worth considering is that, through the use of this equipment, it is possible to get a carbon footprint certification from private companies or agencies. With this, a salmon farming company can certify its salmon production is clean, making it possible to access tax benefits from the government.
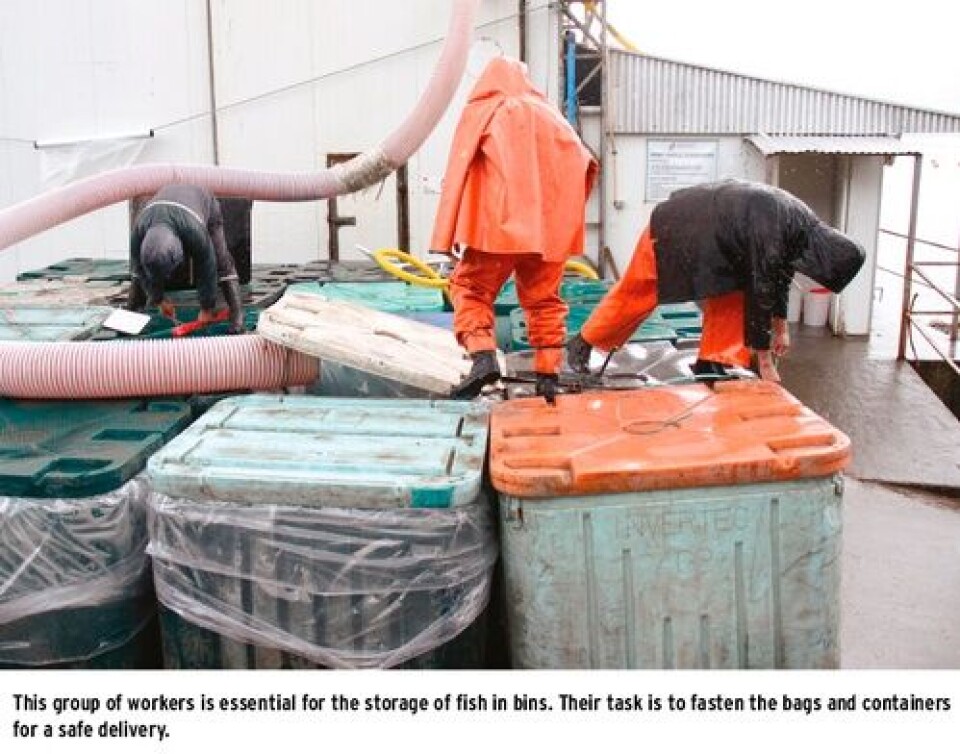
José Manuel Kerber, maintenance chief at Australis Mar, says that among the main benefits provided by the system, the reduction in noise pollution is a very important one .
“Most of the workers want to go to the fish farm pontoons that use wind turbines because they offer highly valued tranquility” Kerber explains.
“For me, one of the main benefits of this technology is the improvement in the quality of life of workers, who, in addition to all the work and normal responsibility of a facility, must also endure the noise of an engine running 24 hours a day, even at bedtime. Other important benefits are fuel economy, lower carbon levels and greenhouse gas emissions into the atmosphere, which helps the environment. This is a factor that has always been a concern for our company, “ Kerber says.
The system uses a bank of 16 to 17 deep cycle batteries, 200 amps each, supplying a daily capacity of 12 to 13 hours of electricity. The gel units auto recharge ability at a certain minimum level -, is a key factor for an efficient operation. They are much more durable than the old lead batteries, previously used by the company. These new deep cycle batteries have a lifetime of approximately 9 years and are maintenance free, unlike the old lead units, which had a lifespan of three years and needed constant maintenance.
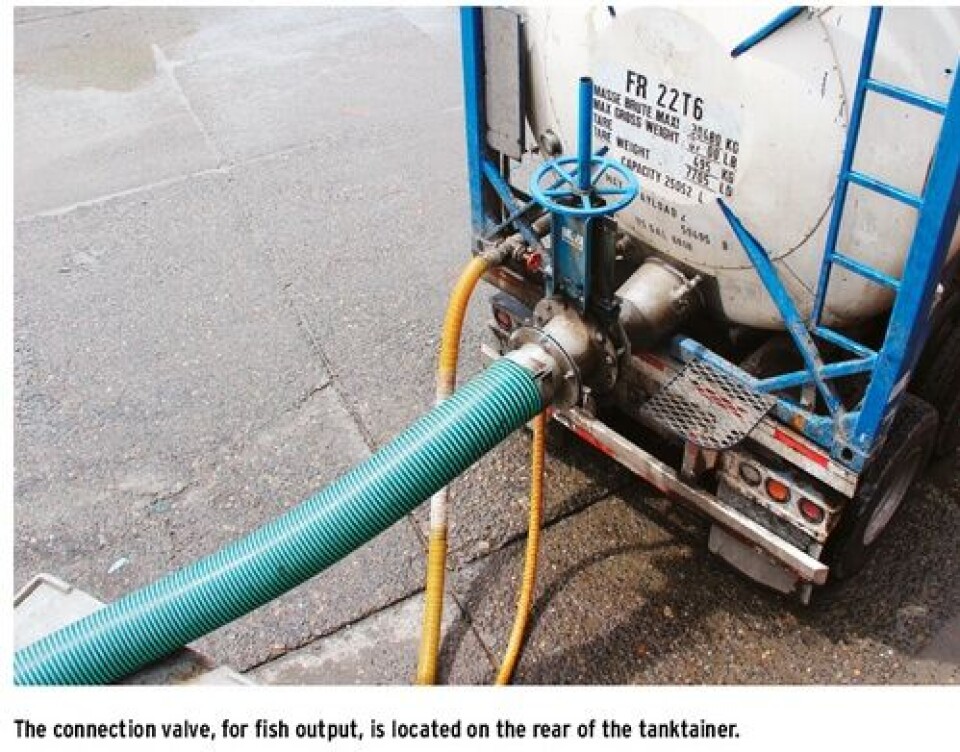
Preventive maintenance is performed by Luxmeter every two months or so. These facilities with the wind turbines are easily spotted at sea.. The system that Luxmeter sells, like most of those used around the world, has an emergency brake system, which is useful in the presence of strong winds, a very common occurrence in these facilities at sea. The turbines are able to withstand winds of up to 180 kilometers per hour.
The amperage controller regulates the power consumption to be generated for the installation by default, so if the blades spin faster it will not supply more power. The inverter is responsible for distributing energy to the entire houseboat transforming current from 48V to 220V.
Kerber explains that most of the sites in Australis Mar keep the wind turbines on during the day, and generally, since they also generate some vibration, they are turned off at night. He continues that they expect to retrieve the money invested in the systems within a period of a year and a half. In winter, the energy required increases andit is necessary to keep the turbines working with the generator at full capacity, since at 5 pm there is no more day light.
In conclusion, wind turbines on fish farm pontoons at Australis Mar, located in the region of Los Lagos and Aysén, are at the forefront of technological development. It has performed well, and presents an outstanding choice in terms of sustainability, cost reduction, quality of life and the relationship between man and the environment. Tanktainers: new fish containers Technology that can leave bins in the past Aaroldo Blaauboer, current head of the commercial division in Asenav, has been working with salmon pumps for nearly two decades and is currently developing a fish storage and pumping system that promises to facilitate tasks in processing plants and farming sites. Asenav works in conjunction with SAAM and is the legal representative of Canavac fish pumps in Chile Over the course of his life, Blaauboer has worked with various technologies to solve some issues in the chilean fish farming industry but, in his own words, what you most want “is bulk fish pumping and handling.” The ultimate goal of the current project, in development since 2004, is the replacement of fish storage bins - by tank trucks. These consist of containers (made of stainless steel in this case) for transporting fish. The container is fixed to a metallic structure on the trailer, and has a holding capacity of 21 m3, 23 m3 or 25 m3. For this technology to succeed, Blaauboer says that that there is only one decisive factor and this is loading and unloading the fish using a pump system. Three years ago, Trusal was the first salmon farming company interested in this new technique.
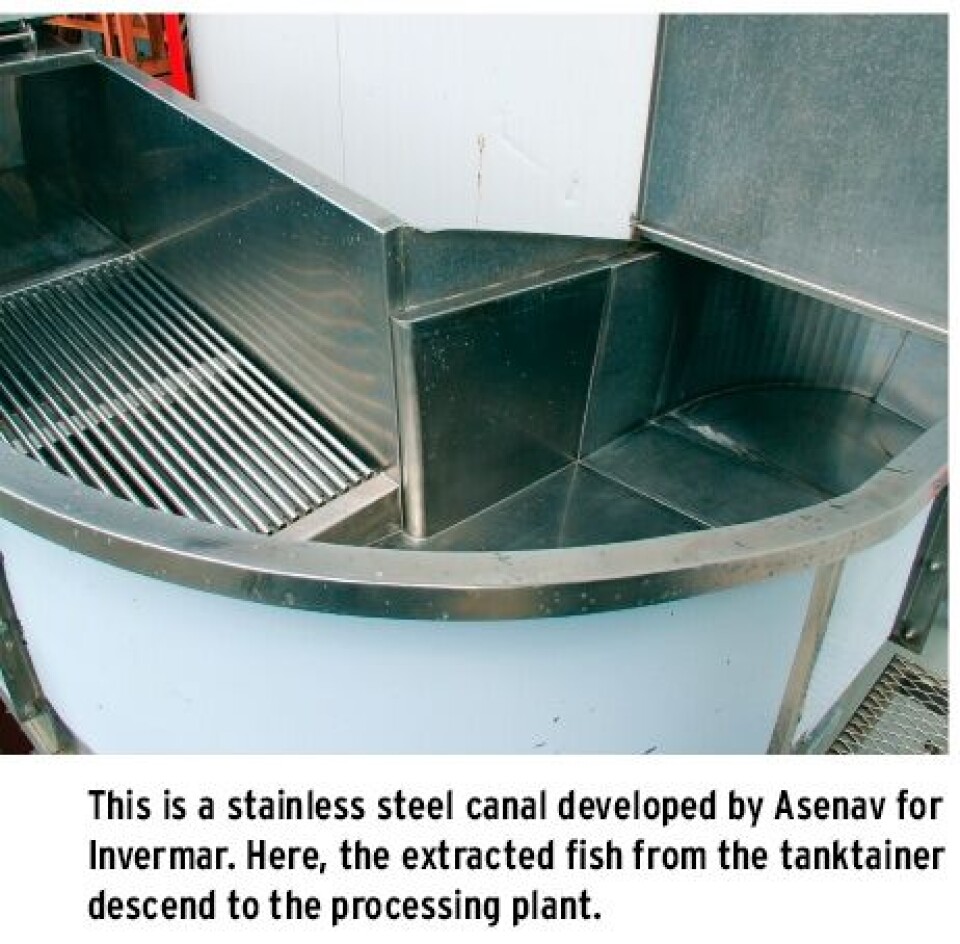
This container was developed some time ago to transport fluids and other products, so its use complies with the necessary legal regulations. Tanktainers can be cleaned without suffering any damage to its internal structure. This is not the case with bins, which begin to show wear and tear scratches and cuts over time and bacteria may lodge in these grooves.
Currently, Invermar carries part of its harvest in two 25 m3 tanktainers. These arrive at the processing plant where the fish are sucked through a tube directly into a stainless steel channel in the plant. The system offered by Asenav includes suction pumps with a diameter of 6, 10 and 12 inches, for harvested fish (there are also smaller dimensions available for smolt). So far, Asenav has sold 19 containers like these to different salmon farming companies in southern Chile.
The larger pump can extract up to 60 tons of fish per hour. This was proved on the wellboat Patagón VII, a vessel equipped with this pump and two tanktainers. The purpose of installing this system on the ship was to unload the fish directly from the warehouse, without the need of a storage facility.
Blaauboer said that the only drawback of his current system is the high cost of the fish pumps, that many companies are not prepared to pay. However, they are an essential component for the proper functioning of the model.
According to Asenav, it is a mistake to think that such tanks can be emptied by gravity without affecting the quality of the fish. Those who have tried this method, are the same people who criticize the performance of the system.
Tanktainers present several advantages compared to the previously used plastic containers, for example, their stainless steel interior and thermal insulation, as well as the fact that they stay completely sealed and lessen operating costs compared to bins, which require bags, seals, a forklift and operator for transport. In addition, bins require preparation before use and more time to be operational, among other negative factors. According to Asenav, in a period of one year no maintenance has been required for the tanktainers, whose lifetime is much longer than that of the bins, which become useless after about one year in use.
According to estimates by the company, a facility that produces about 30,000 tons of product a year must spend $ 110 million to $ 120 million a year just on bags, money which would be saved with the use of tanktainers. Due to the low pumps sales, owing to their high price, Asenav has developed a new equipment called Power Pack, which pressurizes the tank, allowing the fish to be unloaded through this technique. A hose recovers the water and recirculates it to the tanktainer while another pressurizes the interior of the stainless steel container. One of the companies that is testing this technology is Invermar, which has worked with this system since May 2012 at its processing plant in Castro. The company has two leased wellboats of Norwegian origin, allowing the development of a comprehensive harvesting chain and a complete biosecurity process. Invermar explains that the final quality of Atlantic salmon and rainbow trout does not vary between those housed in tanktainers or bins, however, this is not the case of Coho salmon, the final condition of which does improve upon using the new system.
The procedure used at Invermar includes one Power Pack and two tanktainers with air pressure controlled trough a panel, allowing the start of the extraction. This remote control is fitted with start, stop and pause buttons to control the extraction process as well as a pressure regulator.
At this Invermar plant, there is a connection which allows the use of multiple containers in line, however the unloading of fish can only be performed one batch (or tanktainer) at a time. The number of tanks depends on the available space and other production criteria. The advantage of using tanktainers over using bins does not focus only on one area. We have already mentioned that this new technique involves improvements in safety and in terms of health, making the use of bags, seals and other items required by the law for wrappers into bins. obsolete.
Another advantage has to do with the ilegal removal or theft of fish. Bins are vulnerable and have security systems which are easily adulterated, which is not the case with tanktainers, that have an airtight sealing mechanism and a structure much more difficult to penetrate. Also, keep in mind that a single tanktainer has the storage capacity of a whole batch of bins, 26 in total to be exact. This avoids the possibility of confusion or problems with mishandling occurring when storing, counting or entering a batch of 26 bins. One tanktainer delivers a complete batch to the plant in a virtually inviolable container. Bins can present reductions in the number of fish. A batch divided into 26 containers requires more control in yards, to ensure that the entire batch has been processed.
Dino Villella, chief of a processing plant from Invermar in Castro says that “during the process of implementation of this new fish delivering technique, we have been phasing out the use of bins, but not fully. However, in the near future it will no longer be a need to use forklifts or staff to carry out these tasks. With tanktainers the tasks can be performed by one person, unlike the bins, which requires at least three workers”. This reaffirms the aforementioned benefits in terms of cost reduction due to the decrease in the number of inputs and manpower required.
There are four salmon farming companies in Puerto Montt and two in Chiloé who are opting for this technology. The only difference between them is the type of tanktainer they use (materials and dimensions). Invermar uses 25 m3 tanks, which work perfectly with the species the company currently produces, namely Atlantic and coho salmon.
The 25 m3 tank is supported and fixed to the trolley by a steel frame structure welded to the tanktainer. Invermar includes two trestles that provide additional support and security to the container when loading and unloading fish, a preventive measure in case the “legs” that support the tanktainers collapse.
Invermar rents the tanktainers (developed by Asenav) to SAAM, and in Villella words “with the money saved in inputs, we are able to pay the tanktainer rent.” He also said that “we will determine whether to purchase or keep renting the tanks in the future, but according to the current results, this technology would continue to be in use. Only in inputs we save from ten to twelve dollars per ton. “
The ice needed inside the tanktainer to transport the cargo currently represents almost the same cost compared to the previous system, and is arranged at a ratio of (in the case of Invermar) 0.6 liters per kilo of fish. The company considers that the best product for these purposes is the flow ice, used in a ratio of 6:4 (ice and water, respectively). This compound keeps the tankat a lower temperature and for longer than other products, in addition to being homogeneous, which prevents fish from being crushed by the weight of the specimens above them, thus undermining the meat quality.
Tanktainers can keep fish at a stable temperature of -1°C for a period of 24 hours without complications (using ice flow), a situation not possible in the bins, where during this period of time, the interior temperature can vary between 1°C and 2°C.
Harvested fish transportation costs also remain unchanged, however, according to Invermar, it is possible to increase the biomass inside the tanks to make the service more profitable. They can switch from 450kg salmon/m3 (which is the current density used in tanktainers and bins) to 600 kg salmon/m3, but this volume still has to be studied.
With a truck, it takes between 1 hour 20 minutes to an hour and a half to receive the whole batch of bins. This is clearly a greater time range than the time needed with a tanktainer, which normally is ready to deliver the load in an hour. Coho salmon processed by Invermar last month showed 15 percent of relative desquamation in tanktainers and 28 percent in bins, representing a significant difference. Most of the plants working with bins today, have bin tumblers in conjunction with lifting belts to transport the fish. These usually cause damage to Pacific salmon. According to Invermar, this does not happen with the new system implemented by Asenav that extracts the salmonid from the tank through a hose and then drops them into a smooth stainless steel channel, through which the fish flow without suffering any damage.
At present Asenav is developing a system for automated cleaning and disinfection of tanktainers. These are currently sanitized manually, with a pressure washer. The Company believes that there are still many similar improvements possible in the short and medium term. Such is the case of the implementation of a quick connection for the output of fish from the container, eliminating the need of bolts and optimizing and improving service time.
Salmonid production at industrial level has faced several challenges since its inception, which have demanded both science and technology to work together in order to solve the problems that occur.
Chile has an important role in the global salmon farming industry, being the second largest producer after Norway. The opening of new markets, the stagnation of other ones, new scenarios filled with changes, fluctuating prices and rising production volumes, are some of the challenges that require the implementation of new technologies to be turned into opportunities and not failures.
This is where the initiatives by Storvik Chile, Luxmeter Energy, and Asenav together with SAAM, result not only in immediate solutions, but also provide some of the gears that will keep the development engine running, allowing inventiveness to resolve conflicts and serving as a key to the future of the industry, with all that this involves at a national and global level.